中国航天科工二院:里程碑!实现飞行器产品复杂结构的3D打印集成制造!
时间:2021-09-02 08:45 来源:中国航天科工二院 作者:admin 阅读:次
中国航天科工集团二院第二总体设计部(简称二部)始建于1958年,是我国组建最早的从事尖端科学技术与研制的单位,是我国最为重要的导弹武器系统研制、生产单位和空天防御事业发展的领军单位。8月27日,二院二部发布消息称实现了某型飞行器产品复杂结构的3D打印集成制造,并指出这是3D打印技术在航天领域飞行器研制中的重要里程碑,进一步提升了飞行器轻量化水平,为未来新一代飞行器发展提供了有力支撑。
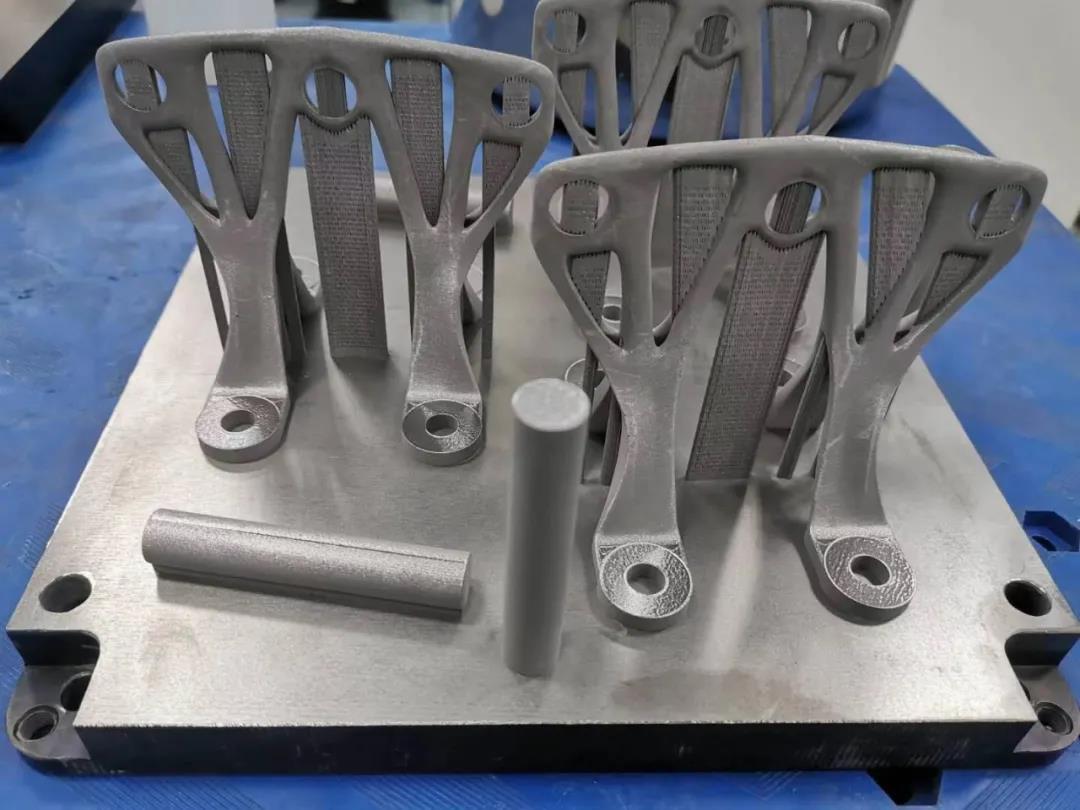
中国航天科工集团二院二部实现某型飞行器产品复杂结构3D打印集成制造。 图片来源:中国航天科工集团二院二部供图
飞行器结构产品“无模具”制造,生产效率提高了一倍,在确保性能不下降的基础上,成本降低近一半,解决了传统生产模式中加工时间长、质量管控难度大、成本高等难题,通过3D打印一体化成型技术,数字化制造能力大幅提升。
二部专家介绍,航天飞行器产品结构零部件多,生产周期长、成本高。此前,一套复杂结构产品的部件常常由数十个零件组成,每个零件都要建立三维模型并设计“个性化”的工艺流程,随后在数字机床上逐一进行生产加工,生产周期往往按月计算。同时,由于“车铣刨磨”等传统机加工艺的限制,要让飞行器“瘦身减肥”很困难,直接影响飞行器的性能提升。有时候,结构设计师为了减少几克的重量也是煞费苦心。
如今,通过3D打印技术实现面向增材制造的一体化结构设计与制造,可使复杂部件的零件数大幅减少,通过一体化三维建模后导入3D打印机中直接成型,一台打印机可实现多个零件的同时打印,制造时间从几个月缩短到十余天。同时,随着零件数量的减少,部件装配环节也更简化,
结构可靠性和装配效率大幅提升。
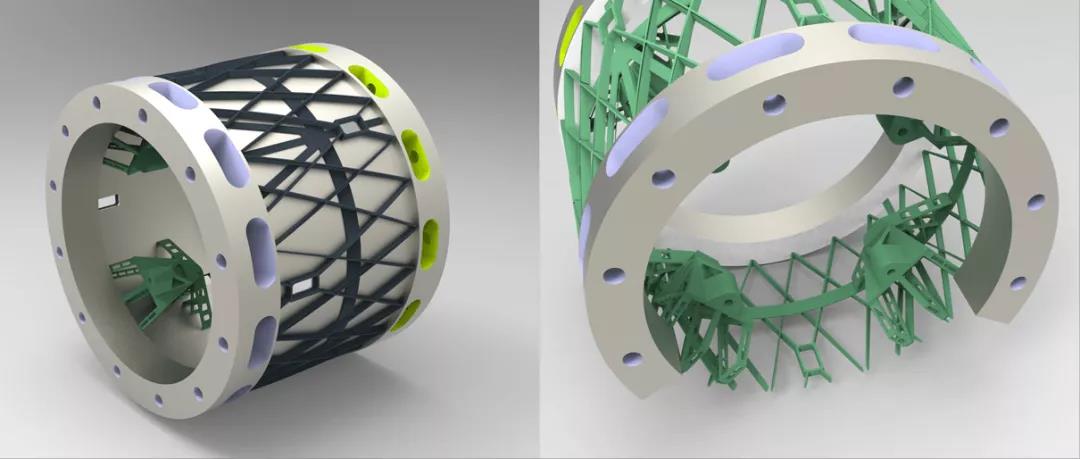
通过基于3D
打印的优化设计,设计师可突破“车铣刨磨”等传统机械加工工艺限制,选择采用网状支撑、空心流道等更加优化的结构形式。相比传统棒料或管料的机加方式,现在可通过“一次成型、少量加工”实现高效生产。针对“一次成型”的3D打印产品,只需要对结构安装面等表面精度要求比较高的局部部位进行少量精加工即完成零件生产,从而大幅提升生产效率。
二部3D打印青年创新工作室负责人金先生表示,团队一直紧跟国内外3D打印技术发展趋势,积极开展新技术、新方法、新工艺的学习与应用,牵头解决了多个项目结构轻量化设计与一体化制造难题,力争为先进飞行器打造更轻、更强、更耐热的“钢筋铁骨”。
3D打印技术是以金属粉末、金属丝为原材料,通过逐层打印、堆积成型的方式实现构件一体化成型的制造技术,涉及数字建模、机电控制、材料科学与工艺技术等多个领域的交叉融合,具有成型精度高、制造周期短、可成型复杂外形和中空结构的特点,可满足航天产品“轻量化、高性能、快速研制”的设计与制造需求,被认为是航天领域未来结构设计与制造技术变革方向之一。
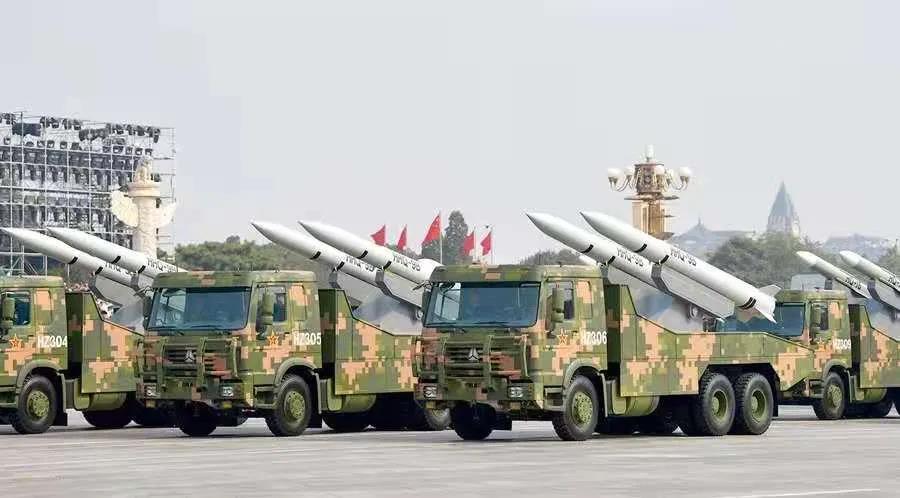
在过去的“十三五”期间,二部紧跟3D打印技术发展步伐,开展面向增材制造的结构产品设计和应用探索,在复杂拓扑结构建模技术、优化仿真分析技术、数字化制造仿真技术、新材料应用等方面开展了研究工作。以“赛”“研”“用”等多种形式,锻炼设计师队伍,多次组织团队参加全国3D打印设计大赛并屡创佳绩。
二部结构室相关负责人表示,科技人员在提高设计应用能力的同时,将经验固化形成《面向增材制造的结构设计手册》等知识成果,使增材制造和优化设计的理念深入人心,并且在项目研制中取得了良好实效。
后续,二部将持续推动基于3D打印技术的优化设计、应用和产品创新,加强一体化结构的设计、分析、制造、性能验证等基础能力建设,促进新一代航天飞行器结构性能提升。
(责任编辑:admin)
最新内容
热点内容