清华大学增材顶刊:基于DIC的电弧增材制造构件全场变形原位测量技术
时间:2023-07-18 16:24 来源:材料科学与工程 作者:admin 阅读:次
电弧定向能量沉积(Arc-based Directed Energy Deposition)技术,又称电弧增材制造(Wire + arc
additive manufacturing,
WAAM),具有沉积效率高、制造成本低、制造周期短及材料利用率高等诸多优势,特别适合大尺寸构件快速成型以及修复再制造,在航空航天、轨道交通、核电等领域具有广泛应用前景。
变形测量和控制是金属增材制造中最重要的问题之一。金属增材制造在高温梯度和大约束条件下发生沉积和凝固,并伴随着复杂的冶金现象和应力演化。应力超过材料屈服强度可能导致构件变形,超过强度极限导致裂纹缺陷甚至断裂。而由于WAAM热输入大,变形和开裂问题更为突出。因此,有必要对WAAM过程中的变形进行监测。
增材制造变形的研究主要通过数值模拟和实验方法。数值模拟主要通过宏观尺度(>10-3 m)下的顺序耦合热弹塑性有限元计算来实现,然而数值模拟和实验测量之间的一致性存在一定误差。实验测量,包括坐标测量和位移传感器。坐标测量(如激光3D扫描)主要用于测量沉积后的零件变形,不能实时测量。而位移传感器(激光位移传感器或DVRT传感器)仅能记录某一点或几个点的变形信息,在全场变形测量方面存在一定局限性。数字图像相关(Digital Image Correlation,DIC)是一种基于光学的测量技术,其基本原理是跟踪变形前后图像中相同子区特征点的位移,从而得到全场变形。
近日,清华大学机械系赵玥副研究员团队采用DIC技术实现了电弧增材制造构件全场变形的原位测量。团队自主设计并搭建了WAAM和三维DIC测量系统,研究了DIC系统测量精度、弧光干扰及屏蔽技术、散斑质量对测量精度的影响,并通过DIC测量与数值模拟方法研究了单臂墙及圆筒型WAAM构件的变形演变规律。相关研究成果以“In situ measurement of full-field deformation for arc-based directed energy deposition via digital image correlation technology”为题,发表于国际增材制造领域顶级期刊《Additive Manufacturing》。论文第一作者为清华大学博士后王强(现为上海交通大学助理研究员),通讯作者为清华大学赵玥副研究员。本研究获得国家自然科学基金支持,未来团队将持续开展DIC应力变形测量技术研究,力争实现电弧增材制造过程构件变形的实时全场测量及在线调控。
论文链接:https://doi.org/10.1016/j.addma.2023.103635
DIC测量系统具有较高的精度,测量误差可控制在微米级,2D-DIC系统静态误差为±4μm,3D-DIC系统静态误差为±6μm。在10mm变形范围内,系统测量误差为0.012mm,0.12%。同时采用2D-DIC与3D-DIC测量相同构件增材过程变形,测量结果保持一致。
WAAM过程中强烈的弧光会严重影响DIC图像质量,电弧覆盖区域图像曝光严重,无法拍摄到散斑,必须采取弧光屏蔽措施。为此设计了平面型弧光挡板及L型弧光挡板。由于挡板不能紧密贴合增材构件,挡板底部仍会泄漏弧光。改为L型挡板并添加石棉布,使挡板与增材构件软接触,能够有效屏蔽弧光,得到高质量DIC图像。
DIC散斑作为记录变形信息的载体,通常有自然散斑和人工散斑两种形式,在2D-DIC应用中,上述两种散斑形式均可得到高质量图像用于DIC变形计算。但在3D-DIC应用中,仅可采用人工散斑。原因是采用构件表面自然纹理作为散斑,当不同角度拍摄照片时,相同位置的反光角度不同,造成图像灰度差异,从而导致相关关系计算失效。
分别通过DIC、激光3D扫描、数值模拟方式获取WAAM圆筒构件外表面轮廓,外轮廓直径沿高度方向的变化趋势保持一直。DIC测量构件上特征点的位移变化与数值模拟变形演变规律相近。DIC技术是WAAM构件全场变形原位测量的有效途径,实现DIC在线实时变形测量与控制对金属增材制造成形控制具有重要意义。
研究结果表明:DIC技术可实现电弧增材制造构件全场变形原位测量,且具有较高的测量精度。对于2D-DIC系统,自然散斑和人工散斑均可用于高精度测量;但是对于3D-DIC,必须采用人工散斑。WAAM过程中强烈的弧光会影响DIC图像质量,必须采取有效的屏蔽措施。使用DIC技术测量的WAAM构件变形与数值模拟、三维激光扫描测量结果具有高度一致性。通过DIC技术,有望实现电弧增材制造过程全场变形的实时测量及调控。
变形测量和控制是金属增材制造中最重要的问题之一。金属增材制造在高温梯度和大约束条件下发生沉积和凝固,并伴随着复杂的冶金现象和应力演化。应力超过材料屈服强度可能导致构件变形,超过强度极限导致裂纹缺陷甚至断裂。而由于WAAM热输入大,变形和开裂问题更为突出。因此,有必要对WAAM过程中的变形进行监测。
增材制造变形的研究主要通过数值模拟和实验方法。数值模拟主要通过宏观尺度(>10-3 m)下的顺序耦合热弹塑性有限元计算来实现,然而数值模拟和实验测量之间的一致性存在一定误差。实验测量,包括坐标测量和位移传感器。坐标测量(如激光3D扫描)主要用于测量沉积后的零件变形,不能实时测量。而位移传感器(激光位移传感器或DVRT传感器)仅能记录某一点或几个点的变形信息,在全场变形测量方面存在一定局限性。数字图像相关(Digital Image Correlation,DIC)是一种基于光学的测量技术,其基本原理是跟踪变形前后图像中相同子区特征点的位移,从而得到全场变形。
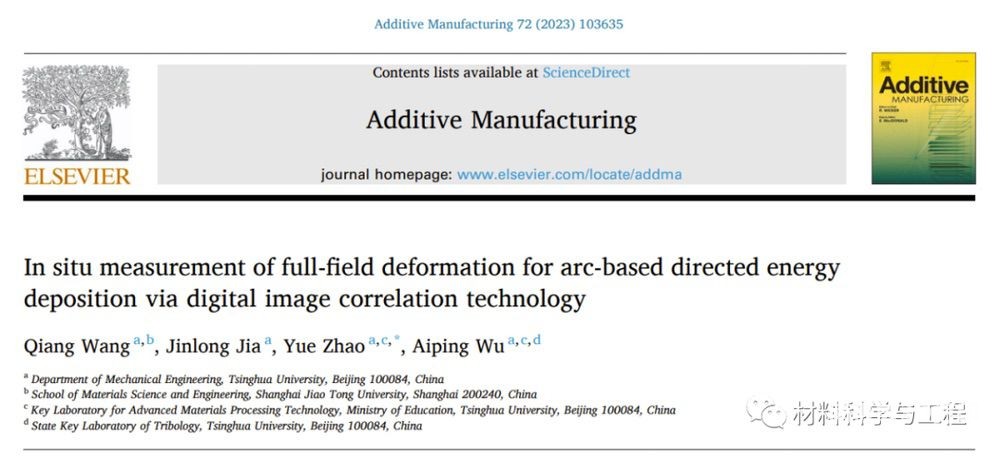
近日,清华大学机械系赵玥副研究员团队采用DIC技术实现了电弧增材制造构件全场变形的原位测量。团队自主设计并搭建了WAAM和三维DIC测量系统,研究了DIC系统测量精度、弧光干扰及屏蔽技术、散斑质量对测量精度的影响,并通过DIC测量与数值模拟方法研究了单臂墙及圆筒型WAAM构件的变形演变规律。相关研究成果以“In situ measurement of full-field deformation for arc-based directed energy deposition via digital image correlation technology”为题,发表于国际增材制造领域顶级期刊《Additive Manufacturing》。论文第一作者为清华大学博士后王强(现为上海交通大学助理研究员),通讯作者为清华大学赵玥副研究员。本研究获得国家自然科学基金支持,未来团队将持续开展DIC应力变形测量技术研究,力争实现电弧增材制造过程构件变形的实时全场测量及在线调控。
论文链接:https://doi.org/10.1016/j.addma.2023.103635
DIC测量系统具有较高的精度,测量误差可控制在微米级,2D-DIC系统静态误差为±4μm,3D-DIC系统静态误差为±6μm。在10mm变形范围内,系统测量误差为0.012mm,0.12%。同时采用2D-DIC与3D-DIC测量相同构件增材过程变形,测量结果保持一致。
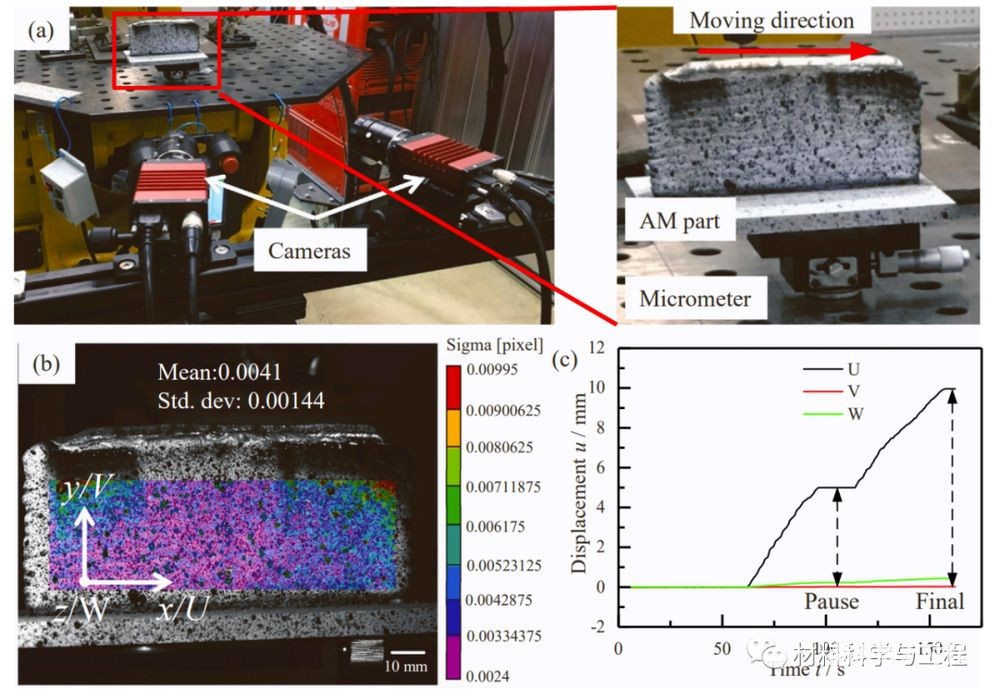
图1 DIC系统测量误差评估:(a)测试平台;(b)图像质量;(c)位移测量分量。
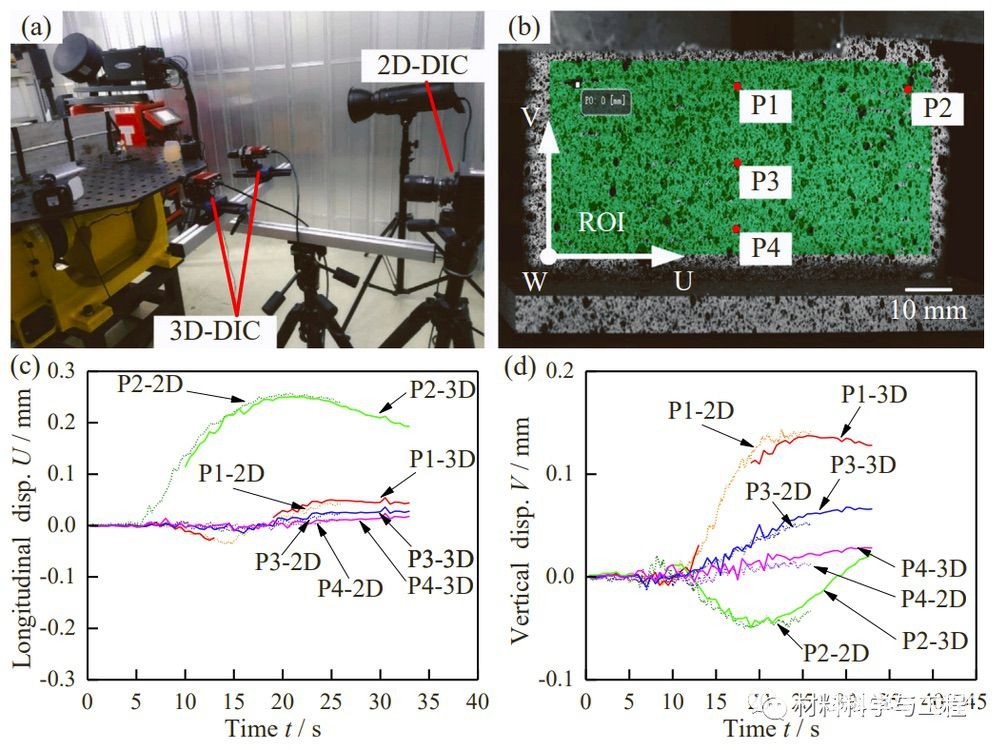
图2 2D-DIC与3D-DIC测量结果对比:(a)试验平台;(b)特征点;(c)纵向位移对比;(d)垂向位移对比。
WAAM过程中强烈的弧光会严重影响DIC图像质量,电弧覆盖区域图像曝光严重,无法拍摄到散斑,必须采取弧光屏蔽措施。为此设计了平面型弧光挡板及L型弧光挡板。由于挡板不能紧密贴合增材构件,挡板底部仍会泄漏弧光。改为L型挡板并添加石棉布,使挡板与增材构件软接触,能够有效屏蔽弧光,得到高质量DIC图像。
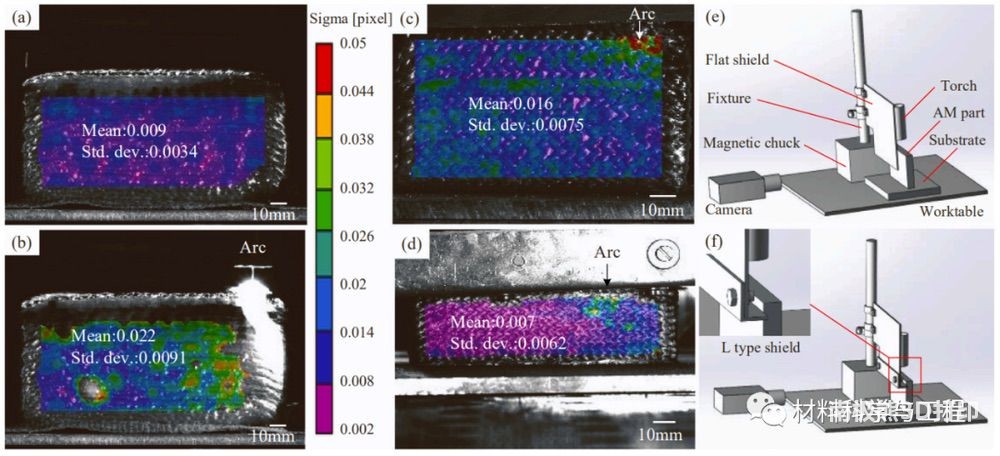
图3 弧光影响及屏蔽措施:(a)无弧光;(b)有弧光无屏蔽;(c)有弧光,平板屏蔽;(d)有弧光,L型挡板屏蔽;(e)平板屏蔽装置;(f)L型挡板屏蔽装置。
DIC散斑作为记录变形信息的载体,通常有自然散斑和人工散斑两种形式,在2D-DIC应用中,上述两种散斑形式均可得到高质量图像用于DIC变形计算。但在3D-DIC应用中,仅可采用人工散斑。原因是采用构件表面自然纹理作为散斑,当不同角度拍摄照片时,相同位置的反光角度不同,造成图像灰度差异,从而导致相关关系计算失效。
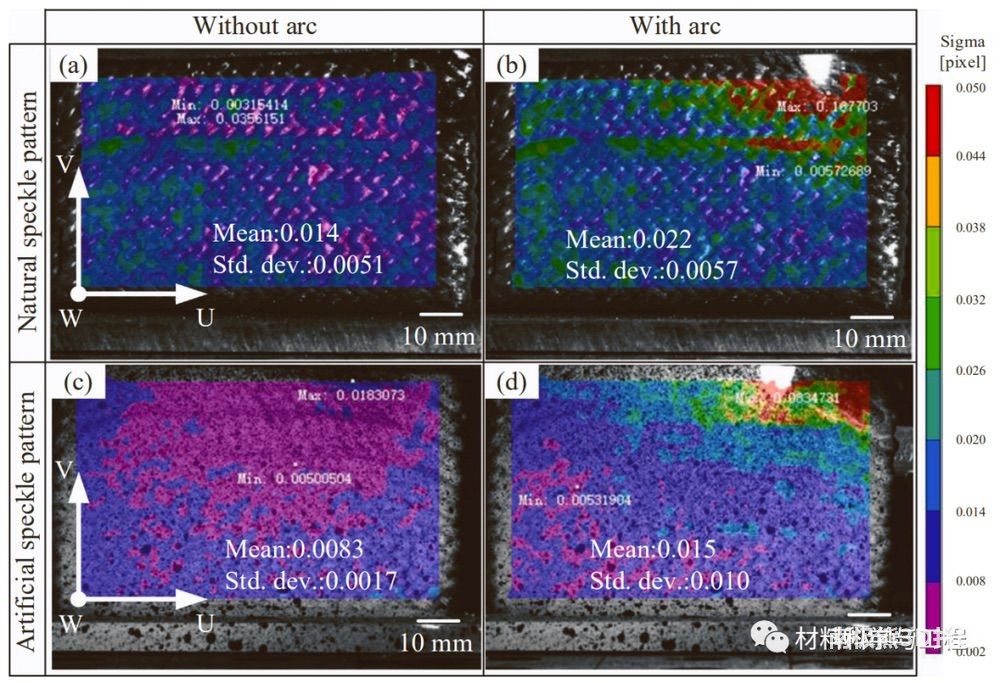
图4 自然散斑与人工散斑对比:(a)无电弧,自然散斑;(b)有点糊,自然散斑;(c)无电弧,人工散斑;(d)有电弧,人工散斑。
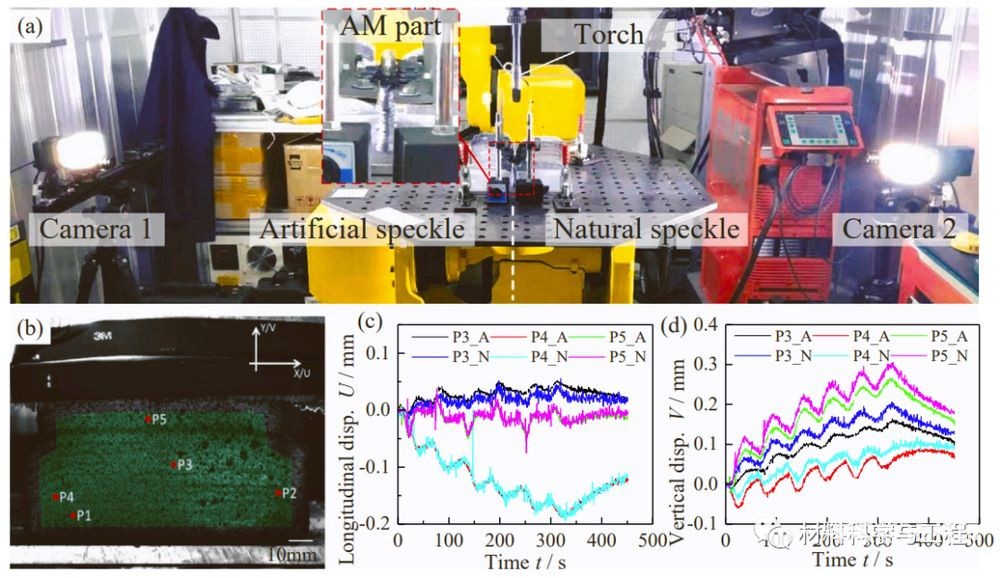
图5 基于2D-DIC系统同时测量自然散斑与人工散斑试样变形:(a)实验装置;(b)特征点位置;(c)纵向位移对比;(d)垂向位移对比。
分别通过DIC、激光3D扫描、数值模拟方式获取WAAM圆筒构件外表面轮廓,外轮廓直径沿高度方向的变化趋势保持一直。DIC测量构件上特征点的位移变化与数值模拟变形演变规律相近。DIC技术是WAAM构件全场变形原位测量的有效途径,实现DIC在线实时变形测量与控制对金属增材制造成形控制具有重要意义。
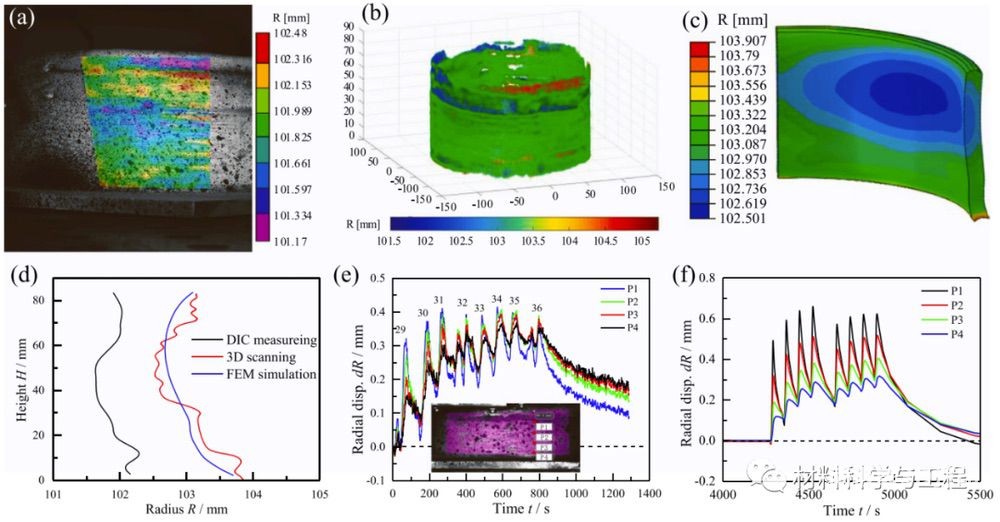
图6 WAAM圆筒构件变形结果及变形演变结果:(a)DIC全场变形;(b)激光3D扫描;(c)数值模拟;(d)外轮廓直径沿高度变化规律;(e)DIC测量特征点位移演变;(f)数值模拟变形演变。
研究结果表明:DIC技术可实现电弧增材制造构件全场变形原位测量,且具有较高的测量精度。对于2D-DIC系统,自然散斑和人工散斑均可用于高精度测量;但是对于3D-DIC,必须采用人工散斑。WAAM过程中强烈的弧光会影响DIC图像质量,必须采取有效的屏蔽措施。使用DIC技术测量的WAAM构件变形与数值模拟、三维激光扫描测量结果具有高度一致性。通过DIC技术,有望实现电弧增材制造过程全场变形的实时测量及调控。
(责任编辑:admin)
最新内容
热点内容