低氮25Cr型双相不锈钢的增材制造保持优异的力学性能
时间:2023-12-27 11:06 来源:增材研究 作者:admin 阅读:次
双相不锈钢(DSS)具有良好的力学性能和耐腐蚀性,在科学技术领域越来越受到关注。然而,作为DSS中的合金元素,N和Cr、Mo等的含量不断增加,增加了生产难度。特别是,N元素增加了Cr2N析出的风险,这会严重恶化DSS的热塑性,同时提高其强度。为此,设计了一种低氮含量的25Cr型DSS,以适应增材制造工艺。
钢铁研究总院团队研究了N含量为0.09wt.%N的低N 25Cr型双相不锈钢的机械性能,屈服强度为712MPa,伸长率为27.5%,而V形缺口冲击韧性为160J/cm2。双相不锈钢(DSS)由铁素体和奥氏体相组成,它们比传统奥氏体不锈钢表现出更高的强度,而与传统奥氏体不锈钢相比,DSS中更高的Cr、Mo和N浓度有助于提高和突出的耐腐蚀性。DSS在某些环境中还表现出独特的抗晶间腐蚀性,使其在石油、化工和海洋等行业中不可替代。与300系列奥氏体不锈钢相比,双相不锈钢可以以类似或更低的成本获得更高的强度和PREN值。
尽管双相不锈钢在性能上比奥氏体不锈钢具有一定的优势,但在广泛应用方面,市场上双相不锈钢完全取代奥氏体不锈钢仍面临挑战。美国材料试验协会(ASTM)的标准中只包括七种类型的铸造双相不锈钢,而锻造双相不锈钢有数百种。凝固后冷却过程中的缓慢冷却过程导致有害的二次沉淀物的形成,如CrN、Cr2N、σ相或χ相,这会显著影响机械性能和耐腐蚀性。这使得在使用传统铸造工艺的复杂结构应用中保持双相不锈钢的性能具有挑战性,这是双相不锈钢应用范围有限的重要原因。
近年来,增材制造技术的发展引入了一种具有极快冷却速率的新金属成型工艺。一次性成型方法减少了模具支出,并允许制造更复杂的结构部件,同时避免了铸件冷却过程中的σ相沉淀和晶粒粗化等问题。增材制造的特点有效地解决了双相不锈钢铸件成型和产品形式多样化的问题。
基于上述研究背景,本工作重点研究了N含量较低(≤0.1wt.%)的2507型双相不锈钢,并利用激光粉末床熔融(L-PBF)方法制备了具有高强度、高塑性和优异韧性的25Cr型DSS。分析了其微观结构在不同阶段的演变,通过控制成分和印刷方法,实现了沉淀强化和晶粒细化的优势。该方法有望为双相不锈钢的应用提供增材制造工艺的替代成分优化策略。
采用氩气雾化法制备了尺寸分布为15–50μm的25Cr型DSS粉末。通过电感耦合等离子体原子发射光谱法(ICP-AES)测量粉末的主要化学成分,结果如表1所示。图1a显示了在扫描电子显微镜(SEM)下观察到的形态;粉末呈现出光滑和圆形,没有卫星颗粒。粉末的X射线衍射(XRD)分析结果如图1b所示,显示99%铁素体和1%奥氏体的相组成,未检测到有害相。
上述粉末用于DLM-280金属3D打印机上的选择性激光熔化(SLM)。在高纯氩气(99.9%)的保护气氛中,在316不锈钢基板上进行构建工艺。具体的打印参数如下:激光输入功率(P)为190W,激光光斑直径为0.1mm,粉末层厚度(h)为0.02mm,扫描间距(t)为0.1mm、扫描速度(v)为850mm/s,以及每层之间具有45°角的双向扫描图案。使用公式计算出的能量密度为117.65J/cm3。
将构建的试样分别在1100、1150和1200°C的温度下进行固溶处理1小时。尺寸为10×10×5mm的立方体样品用于表征微观结构,尺寸为10 x 60×6mm的冲击样品和尺寸为20×70×6mm的拉伸样品用于测试机械性能。冲击试样和拉伸试样的最终尺寸分别如图2a、b所示。采用阿基米德排水法,试样的相对密度为99.87%。
图3a显示了未经热处理的构建立方体试样的微观结构,显示了马赛克状的规则结构。图3b中的放大金相图像进一步揭示了镶嵌状网格结构以规则的图案排列,最小结构单元为100μm。镶嵌单元的核心由较大的晶粒组成,而边缘由类似于再结晶晶粒的较小晶粒组成。这些单元形成的轨道宽度为100μm,沿两个方向排列,彼此成90°角。上述马赛克结构主要是由于特殊的扫描方法,其中激光光斑半径为100微米,扫描线间距也为100微米。由于激光器核心处的能量较高,与边缘处的粉末相比,核心中的粉末接收到更多的能量,导致核心和边缘之间的晶粒尺寸不同。在这一点上,晶粒尺寸分布在芯部呈现较大晶粒,在侧面呈现较小晶粒。随着扫描的进行,在一层完成后,下一层粉末的扫描路径与前一层垂直90°。下一层的激光能量输入在一定程度上影响了前一层已经形成的基体,导致二次加热和再结晶,最终形成网格状结构。试样在1200°C下热处理1小时后的微观结构金相如图3c所示,值得注意的是,热处理后微观结构中的网格状镶嵌结构保持完整和规则,这与先前研究中观察到的热处理后网格状结构的破坏有很大不同。图3d所示的放大微观结构表明,一定量的新相已沉淀在基体相的晶界上,即使在1200°C下热处理1小时后,其尺寸仍然很小。上述微观结构特征主要归因于独特的低氮(N)成分设计。
为了进一步表征热处理前后的微观结构特征,使用EBSD对热处理前后相分布进行统计分析。图4a显示了热处理前激光照射表面的EBSD相位图,其主要由铁素体相组成。这主要是由于扫描过程中的高温和极快的冷却速度,这不允许奥氏体在形成和冷却过程中沉淀。图4b显示了未经热处理的扫描侧的EBSD相位图,可以观察到,每层铁素体都已被激光熔化为宽度约为100μm的固体结构。这种固体结构将提高冲击韧性,稍后将对此进行详细讨论。图4c、e分别显示了在1200°C下热处理1小时后扫描的正面和侧面的相位分布图。大量奥氏体在铁素体的晶界处析出,一些奥氏体在铁素体内的低角度晶界处析出。可以观察到,在晶粒内的高角度晶界上沉淀的奥氏体的尺寸明显大于在低角度晶界上沉积的奥氏体的大小。这主要是因为高角度晶界具有更高的能量,为奥氏体的快速形核和生长提供了便利。图4d显示了在1100°C的较低固溶温度下热处理1小时后扫描前沿的相分布图。可以发现,与1200°C相比,奥氏体的量显著增加,并且奥氏体以带状图案分布,与铁素体的晶界相连。在较低的溶液温度下,奥氏体相的形态特征与在较高溶液温度下的不连续岛状分布相比发生了显著变化。
图5显示了热处理前后样品的拉伸性能。可以观察到,样品在热处理前的状态下具有非常高的屈服强度(920MPa)和拉伸强度(922MPa),但伸长率仅为2%。关于热处理后样品的拉伸性能,可以观察到,随着溶液温度的升高,样品的强度和塑性同时增加。在1200°C下固溶处理后,即使由于N含量仅为0.098%而只有微弱的固溶强化,屈服强度仍高达712MPa。在之前的研究中,标准级(与本文相比,N含量更高)2205和2507双相不锈钢的屈服强度,无论是通过铸造还是增材制造,通常在600至660 MPa之间。本文获得的测试结果表明,在1200°C下固溶处理1小时后,样品的屈服强度显著高于先前研究的实验结果。
表2显示了热处理前后样品的冲击韧性值,与采用类似工艺的2707个BPF样品的冲击性能进行了比较。可以观察到,本研究中实验钢的冲击韧性明显高于参考钢,未处理样品的冲击韧性值明显高于参考结果。尽管未经热处理的样品在拉伸过程中仅表现出2%的伸长率,但它们表现出高韧性值。图6a–c显示了不同尺度下未处理样品断裂表面的SEM图像。独特的断裂形态是试样韧性值较高的重要原因。从图6a中的宏观断裂形态可以观察到,样品的断裂表面分为两侧。靠近V形缺口的一侧(较白的一侧)显示出不规则的解理断裂,而另一侧显示出与其微观结构相似的镶嵌状结构。图6b、c中的放大图像更清楚地显示了复杂的断裂形式。在每个小的结构单元中,中心大晶粒呈现出光滑的解理断裂面。结构单元边缘的小晶粒区域由一定数量的较小凹坑组成。该区域较小的晶粒尺寸和多个界面部分阻碍了裂纹在压裂过程中的扩展,从而提高了抗冲击性。另一方面,如前所述,样品侧的微观结构由整体垂直排列的铁素体组成。裂纹只能通过这些铁素体区域内的穿晶断裂传播,从而形成与前表面的网格状结构外观相似的断裂表面。不同晶粒尺寸的混合微观结构的共存,以及侧面结构中铁素体的完整性,有助于样品的复杂断裂形式和高韧性值。
热处理冲击样品断裂表面的SEM图像如图6d–f所示。图6d中的宏观图像显示了一个具有光滑边缘和不均匀核心的复合结构。图6e中核心区域的放大图像显示了凹坑和解理面的组合,一些区域仍显示出网格状结构。图6f中断裂边缘的放大图像显示了解理面。断裂表面不同区域之间的结构差异表明,在断裂过程中,裂纹扩展的连续性相对较差,最终导致对冲击韧性的更客观的测量。
未处理样品的极端拉伸行为主要是由于在未处理状态下存在铁素体结构。通常,在室温下,氮在铁素体中的饱和溶解度为0.007%,而组合物中0.098%的氮大部分溶解在铁素体内,由于氮过饱和导致铁素体晶格畸变。此外,打印过程中的重复加热和快速冷却会导致显著的残余热应力。这些因素的组合导致未处理样品的塑性低和强度高。未处理样品的TEM表征证实了上述推断。图7a显示了TEM尺度下铁素体的内部结构。可以观察到,未变形铁素体的内部是高度无序的。图7b中的放大图清楚地显示了铁素体晶粒内大量随机分布和缠结的位错。即使没有变形,这种状态下的铁素体也会受到显著的内应力,因此,只有少量变形(2%)就会断裂。
如前所述,在1200°C下热处理1小时后,样品的屈服强度达到712 MPa,同时仍保持27.5%的伸长率。这种反常的力学性能主要是由于特殊成分下奥氏体独特的相形态和高温氧化物相的析出共同作用。在较低的溶液温度下,奥氏体含量较高,大量奥氏体沿着铁素体晶界形成连续带。较软且含量较高的奥氏体导致屈服强度降低,晶界上的大分布容易导致两相之间的变形失配,导致断裂。相反,在较高的溶液温度下,奥氏体含量较低,并且沿铁素体晶界呈岛状离散分布。因此,具有较小尺寸和离散分布的奥氏体较少,其通过钉扎在铁素体晶界上而起到第二相增强的作用,从而实现增强的强度和塑性。
此外,在之前的研究中,将高温氧化物Al2O3引入系统中也会提高强度。在传统的铸造工艺中,高温形成的Al2O3在缓慢冷却过程中容易生长并产生夹杂物,难以消除。然而,在增材制造工艺中,极快的冷却速度阻止了这些高温形成的Al2O3的生长,并且它们最终成为有利于机械性能的沉淀物。在这项研究中,TEM观察还显示出精细分散的圆形Al2O3沉淀物,如图8a所示。图8b中的暗场TEM图像提供了Al2O3广泛变化的分布尺寸的更清晰视图。为了更好地说明沉淀物的类型,图8c显示了该区域的EDS图谱结果。很明显,在沉淀物中存在Al和O元素的聚集。这种类型的沉淀强化也是样品较高屈服强度背后的原因之一。我们还使用TEM表征了样品在拉伸断裂后的均匀变形区。图8d显示了变形状态的TEM图像,其中大量位错被铁素体中的小Al2O3夹杂物钉扎。Al2O3颗粒的细分散体和位错之间的相互作用阻碍了铁素体在变形过程中的初始运动,与正常条件下相比,这有助于获得更高的屈服强度。
总之,通过一种独特的成分设计,打破了2507中传统的0.24–0.32%氮(N)含量,形成了独特的奥氏体相形态,同时保持了规则的晶格结构。随着氧化物沉淀物的增强,样品表现出712MPa的高屈服强度,同时仍保持27.5%的良好伸长率。
在本研究中,通过L-PBF方法制备了用于增材制造工艺的低N 25Cr型双相不锈钢。该产品具有优异的强度和延展性。主要结论如下:
1.当采用层扫描方向交替为45°的策略时,试样的微观结构呈现出规则的镶嵌结构。热处理前的微观结构由单个铁素体相组成。在1200°C下热处理后,在铁素体晶界处析出离散且细小的奥氏体,并保留规则的镶嵌结构。
2.特殊的低氮成分设计导致奥氏体相的独特形态,加上氧化物沉淀的强化作用,使本研究中的实验钢在热处理后具有712MPa的高屈服强度,同时保持了27.5%的良好伸长率。
3.增材制造低N 25Cr型DSS的试样表现出优异的V形缺口冲击性能,热处理前的韧性值为98.75J/cm2,热处理后的韧性值约为160J/cm2。
相关论文
Maintaining Excellent Mechanical Properties via Additive Manufacturing of Low-N 25Cr-Type Duplex Stainless Steel
相关链接
https://doi.org/10.3390/ma16227125
钢铁研究总院团队研究了N含量为0.09wt.%N的低N 25Cr型双相不锈钢的机械性能,屈服强度为712MPa,伸长率为27.5%,而V形缺口冲击韧性为160J/cm2。双相不锈钢(DSS)由铁素体和奥氏体相组成,它们比传统奥氏体不锈钢表现出更高的强度,而与传统奥氏体不锈钢相比,DSS中更高的Cr、Mo和N浓度有助于提高和突出的耐腐蚀性。DSS在某些环境中还表现出独特的抗晶间腐蚀性,使其在石油、化工和海洋等行业中不可替代。与300系列奥氏体不锈钢相比,双相不锈钢可以以类似或更低的成本获得更高的强度和PREN值。
尽管双相不锈钢在性能上比奥氏体不锈钢具有一定的优势,但在广泛应用方面,市场上双相不锈钢完全取代奥氏体不锈钢仍面临挑战。美国材料试验协会(ASTM)的标准中只包括七种类型的铸造双相不锈钢,而锻造双相不锈钢有数百种。凝固后冷却过程中的缓慢冷却过程导致有害的二次沉淀物的形成,如CrN、Cr2N、σ相或χ相,这会显著影响机械性能和耐腐蚀性。这使得在使用传统铸造工艺的复杂结构应用中保持双相不锈钢的性能具有挑战性,这是双相不锈钢应用范围有限的重要原因。
近年来,增材制造技术的发展引入了一种具有极快冷却速率的新金属成型工艺。一次性成型方法减少了模具支出,并允许制造更复杂的结构部件,同时避免了铸件冷却过程中的σ相沉淀和晶粒粗化等问题。增材制造的特点有效地解决了双相不锈钢铸件成型和产品形式多样化的问题。
基于上述研究背景,本工作重点研究了N含量较低(≤0.1wt.%)的2507型双相不锈钢,并利用激光粉末床熔融(L-PBF)方法制备了具有高强度、高塑性和优异韧性的25Cr型DSS。分析了其微观结构在不同阶段的演变,通过控制成分和印刷方法,实现了沉淀强化和晶粒细化的优势。该方法有望为双相不锈钢的应用提供增材制造工艺的替代成分优化策略。
采用氩气雾化法制备了尺寸分布为15–50μm的25Cr型DSS粉末。通过电感耦合等离子体原子发射光谱法(ICP-AES)测量粉末的主要化学成分,结果如表1所示。图1a显示了在扫描电子显微镜(SEM)下观察到的形态;粉末呈现出光滑和圆形,没有卫星颗粒。粉末的X射线衍射(XRD)分析结果如图1b所示,显示99%铁素体和1%奥氏体的相组成,未检测到有害相。
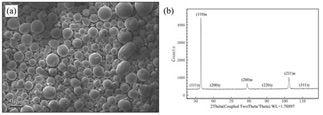
图1。粉末形态和相信息:(a)粉末SEM图像,(b)XRD衍射图。
表1。25Cr型DSS粉末的化学成分1。

通过红外吸收法测定了S、C和O元素。
上述粉末用于DLM-280金属3D打印机上的选择性激光熔化(SLM)。在高纯氩气(99.9%)的保护气氛中,在316不锈钢基板上进行构建工艺。具体的打印参数如下:激光输入功率(P)为190W,激光光斑直径为0.1mm,粉末层厚度(h)为0.02mm,扫描间距(t)为0.1mm、扫描速度(v)为850mm/s,以及每层之间具有45°角的双向扫描图案。使用公式计算出的能量密度为117.65J/cm3。
将构建的试样分别在1100、1150和1200°C的温度下进行固溶处理1小时。尺寸为10×10×5mm的立方体样品用于表征微观结构,尺寸为10 x 60×6mm的冲击样品和尺寸为20×70×6mm的拉伸样品用于测试机械性能。冲击试样和拉伸试样的最终尺寸分别如图2a、b所示。采用阿基米德排水法,试样的相对密度为99.87%。
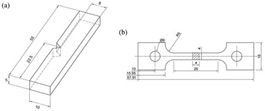
图2:用于测试机械性能的试样尺寸:(a)冲击试样尺寸;(b)拉伸试样尺寸(单位:mm)。
图3a显示了未经热处理的构建立方体试样的微观结构,显示了马赛克状的规则结构。图3b中的放大金相图像进一步揭示了镶嵌状网格结构以规则的图案排列,最小结构单元为100μm。镶嵌单元的核心由较大的晶粒组成,而边缘由类似于再结晶晶粒的较小晶粒组成。这些单元形成的轨道宽度为100μm,沿两个方向排列,彼此成90°角。上述马赛克结构主要是由于特殊的扫描方法,其中激光光斑半径为100微米,扫描线间距也为100微米。由于激光器核心处的能量较高,与边缘处的粉末相比,核心中的粉末接收到更多的能量,导致核心和边缘之间的晶粒尺寸不同。在这一点上,晶粒尺寸分布在芯部呈现较大晶粒,在侧面呈现较小晶粒。随着扫描的进行,在一层完成后,下一层粉末的扫描路径与前一层垂直90°。下一层的激光能量输入在一定程度上影响了前一层已经形成的基体,导致二次加热和再结晶,最终形成网格状结构。试样在1200°C下热处理1小时后的微观结构金相如图3c所示,值得注意的是,热处理后微观结构中的网格状镶嵌结构保持完整和规则,这与先前研究中观察到的热处理后网格状结构的破坏有很大不同。图3d所示的放大微观结构表明,一定量的新相已沉淀在基体相的晶界上,即使在1200°C下热处理1小时后,其尺寸仍然很小。上述微观结构特征主要归因于独特的低氮(N)成分设计。
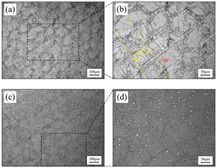
图3。热处理前后试样的光学显微镜(OM)图像:(a)在100倍放大倍率下热处理前的试样,(b)(a)中所选区域的放大微观结构,(c)在1200°c下以100倍放大倍数热处理1小时的试样,以及(d)(c)中所选择区域的放大微结构。
为了进一步表征热处理前后的微观结构特征,使用EBSD对热处理前后相分布进行统计分析。图4a显示了热处理前激光照射表面的EBSD相位图,其主要由铁素体相组成。这主要是由于扫描过程中的高温和极快的冷却速度,这不允许奥氏体在形成和冷却过程中沉淀。图4b显示了未经热处理的扫描侧的EBSD相位图,可以观察到,每层铁素体都已被激光熔化为宽度约为100μm的固体结构。这种固体结构将提高冲击韧性,稍后将对此进行详细讨论。图4c、e分别显示了在1200°C下热处理1小时后扫描的正面和侧面的相位分布图。大量奥氏体在铁素体的晶界处析出,一些奥氏体在铁素体内的低角度晶界处析出。可以观察到,在晶粒内的高角度晶界上沉淀的奥氏体的尺寸明显大于在低角度晶界上沉积的奥氏体的大小。这主要是因为高角度晶界具有更高的能量,为奥氏体的快速形核和生长提供了便利。图4d显示了在1100°C的较低固溶温度下热处理1小时后扫描前沿的相分布图。可以发现,与1200°C相比,奥氏体的量显著增加,并且奥氏体以带状图案分布,与铁素体的晶界相连。在较低的溶液温度下,奥氏体相的形态特征与在较高溶液温度下的不连续岛状分布相比发生了显著变化。
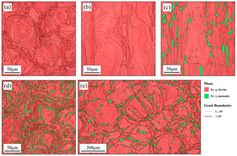
图4。EBSD相位分布图:热处理前试样。
图5显示了热处理前后样品的拉伸性能。可以观察到,样品在热处理前的状态下具有非常高的屈服强度(920MPa)和拉伸强度(922MPa),但伸长率仅为2%。关于热处理后样品的拉伸性能,可以观察到,随着溶液温度的升高,样品的强度和塑性同时增加。在1200°C下固溶处理后,即使由于N含量仅为0.098%而只有微弱的固溶强化,屈服强度仍高达712MPa。在之前的研究中,标准级(与本文相比,N含量更高)2205和2507双相不锈钢的屈服强度,无论是通过铸造还是增材制造,通常在600至660 MPa之间。本文获得的测试结果表明,在1200°C下固溶处理1小时后,样品的屈服强度显著高于先前研究的实验结果。
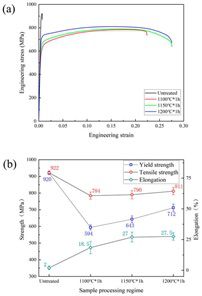
图5。试样的拉伸性能:(a)应力-应变曲线,(b)不同处理状态下的屈服强度、拉伸强度和伸长率。
表2显示了热处理前后样品的冲击韧性值,与采用类似工艺的2707个BPF样品的冲击性能进行了比较。可以观察到,本研究中实验钢的冲击韧性明显高于参考钢,未处理样品的冲击韧性值明显高于参考结果。尽管未经热处理的样品在拉伸过程中仅表现出2%的伸长率,但它们表现出高韧性值。图6a–c显示了不同尺度下未处理样品断裂表面的SEM图像。独特的断裂形态是试样韧性值较高的重要原因。从图6a中的宏观断裂形态可以观察到,样品的断裂表面分为两侧。靠近V形缺口的一侧(较白的一侧)显示出不规则的解理断裂,而另一侧显示出与其微观结构相似的镶嵌状结构。图6b、c中的放大图像更清楚地显示了复杂的断裂形式。在每个小的结构单元中,中心大晶粒呈现出光滑的解理断裂面。结构单元边缘的小晶粒区域由一定数量的较小凹坑组成。该区域较小的晶粒尺寸和多个界面部分阻碍了裂纹在压裂过程中的扩展,从而提高了抗冲击性。另一方面,如前所述,样品侧的微观结构由整体垂直排列的铁素体组成。裂纹只能通过这些铁素体区域内的穿晶断裂传播,从而形成与前表面的网格状结构外观相似的断裂表面。不同晶粒尺寸的混合微观结构的共存,以及侧面结构中铁素体的完整性,有助于样品的复杂断裂形式和高韧性值。
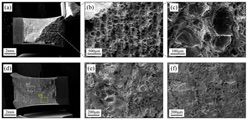
图6。冲击断口的SEM图像:热处理前试样的断口形貌(a)和选区扩大(b,c),在1200°下热处理1小时的试样的断口形态(d),以及选区扩大(e,f)。
表2。V型缺口冲击韧性。
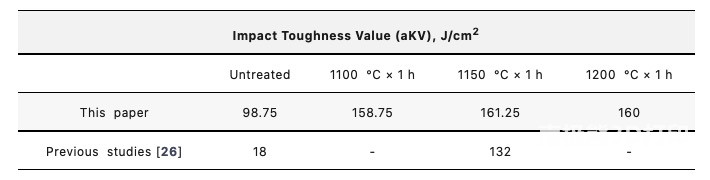
热处理冲击样品断裂表面的SEM图像如图6d–f所示。图6d中的宏观图像显示了一个具有光滑边缘和不均匀核心的复合结构。图6e中核心区域的放大图像显示了凹坑和解理面的组合,一些区域仍显示出网格状结构。图6f中断裂边缘的放大图像显示了解理面。断裂表面不同区域之间的结构差异表明,在断裂过程中,裂纹扩展的连续性相对较差,最终导致对冲击韧性的更客观的测量。
未处理样品的极端拉伸行为主要是由于在未处理状态下存在铁素体结构。通常,在室温下,氮在铁素体中的饱和溶解度为0.007%,而组合物中0.098%的氮大部分溶解在铁素体内,由于氮过饱和导致铁素体晶格畸变。此外,打印过程中的重复加热和快速冷却会导致显著的残余热应力。这些因素的组合导致未处理样品的塑性低和强度高。未处理样品的TEM表征证实了上述推断。图7a显示了TEM尺度下铁素体的内部结构。可以观察到,未变形铁素体的内部是高度无序的。图7b中的放大图清楚地显示了铁素体晶粒内大量随机分布和缠结的位错。即使没有变形,这种状态下的铁素体也会受到显著的内应力,因此,只有少量变形(2%)就会断裂。
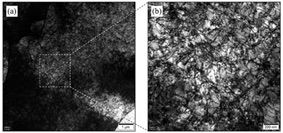
图7。热处理前样品的TEM图像(a)和所选区域放大(b)。
如前所述,在1200°C下热处理1小时后,样品的屈服强度达到712 MPa,同时仍保持27.5%的伸长率。这种反常的力学性能主要是由于特殊成分下奥氏体独特的相形态和高温氧化物相的析出共同作用。在较低的溶液温度下,奥氏体含量较高,大量奥氏体沿着铁素体晶界形成连续带。较软且含量较高的奥氏体导致屈服强度降低,晶界上的大分布容易导致两相之间的变形失配,导致断裂。相反,在较高的溶液温度下,奥氏体含量较低,并且沿铁素体晶界呈岛状离散分布。因此,具有较小尺寸和离散分布的奥氏体较少,其通过钉扎在铁素体晶界上而起到第二相增强的作用,从而实现增强的强度和塑性。
此外,在之前的研究中,将高温氧化物Al2O3引入系统中也会提高强度。在传统的铸造工艺中,高温形成的Al2O3在缓慢冷却过程中容易生长并产生夹杂物,难以消除。然而,在增材制造工艺中,极快的冷却速度阻止了这些高温形成的Al2O3的生长,并且它们最终成为有利于机械性能的沉淀物。在这项研究中,TEM观察还显示出精细分散的圆形Al2O3沉淀物,如图8a所示。图8b中的暗场TEM图像提供了Al2O3广泛变化的分布尺寸的更清晰视图。为了更好地说明沉淀物的类型,图8c显示了该区域的EDS图谱结果。很明显,在沉淀物中存在Al和O元素的聚集。这种类型的沉淀强化也是样品较高屈服强度背后的原因之一。我们还使用TEM表征了样品在拉伸断裂后的均匀变形区。图8d显示了变形状态的TEM图像,其中大量位错被铁素体中的小Al2O3夹杂物钉扎。Al2O3颗粒的细分散体和位错之间的相互作用阻碍了铁素体在变形过程中的初始运动,与正常条件下相比,这有助于获得更高的屈服强度。
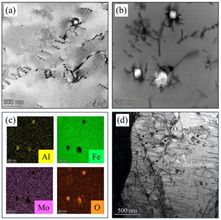
图8。在1200°C下热处理1小时后,试样中氧化物夹杂物的TEM显微照片:(a)未变形状态,(b)(a,C)变形状态的暗场图像,(a,d)变形状态下的EDS图谱。
总之,通过一种独特的成分设计,打破了2507中传统的0.24–0.32%氮(N)含量,形成了独特的奥氏体相形态,同时保持了规则的晶格结构。随着氧化物沉淀物的增强,样品表现出712MPa的高屈服强度,同时仍保持27.5%的良好伸长率。
在本研究中,通过L-PBF方法制备了用于增材制造工艺的低N 25Cr型双相不锈钢。该产品具有优异的强度和延展性。主要结论如下:
1.当采用层扫描方向交替为45°的策略时,试样的微观结构呈现出规则的镶嵌结构。热处理前的微观结构由单个铁素体相组成。在1200°C下热处理后,在铁素体晶界处析出离散且细小的奥氏体,并保留规则的镶嵌结构。
2.特殊的低氮成分设计导致奥氏体相的独特形态,加上氧化物沉淀的强化作用,使本研究中的实验钢在热处理后具有712MPa的高屈服强度,同时保持了27.5%的良好伸长率。
3.增材制造低N 25Cr型DSS的试样表现出优异的V形缺口冲击性能,热处理前的韧性值为98.75J/cm2,热处理后的韧性值约为160J/cm2。
相关论文
Maintaining Excellent Mechanical Properties via Additive Manufacturing of Low-N 25Cr-Type Duplex Stainless Steel
相关链接
https://doi.org/10.3390/ma16227125
(责任编辑:admin)
最新内容
热点内容