激光粉末床熔合增材制造中表面纹理与内部缺陷的相关性
时间:2023-01-17 20:25 来源:长三角G60激光联盟 作者:admin 阅读:次
据悉,本研究旨在研究激光束粉末床熔合(LB-PBF)零件的表面纹理与内部缺陷或密度之间的相关性。
在金属增材制造技术的实施过程中,现场监控和反馈控制系统的可用性确保了高质量的成品零件的制造。本研究旨在研究激光束粉末床熔合(LB-PBF)零件的表面纹理与内部缺陷或密度之间的相关性。在本研究中,通过将LB-PBF工艺应用于In 718镍合金粉末,制备了120个立方试样。根据ISO 25178–2标准,确定了制造样品的密度和35个表面纹理参数。使用统计方法,观察到区域表面纹理参数与试样内的密度或内部缺陷之间存在很强的相关性。对这些区域表面纹理参数的现场监测可以有助于将其用作反馈系统中的控制变量。
介绍
金属增材制造(AM),尤其是粉末床熔合(PBF),被认为是创造具有精致材料性能和复杂结构的新材料的重要过程。该工艺涉及使用激光或电子束作为热源。然而,人们对使用PBF工艺获得的成品零件的质量提出了一些担忧。这些问题涉及到成品零件中出现气孔和未熔合等缺陷,以及由于PBF工艺固有的特性导致加工过程中表面粗糙度的增加。因此,发现PBF制造零件的机械性能和表面粗糙度低于锻造材料。因此,为了尽量减少PBF加工过程中缺陷的发生并确保成品零件的高质量,开发了监控和反馈控制系统。
使用传统的制造技术,如粉末冶金、轧制、焊接、化学气相沉积和扩散连接,很难制造具有复杂几何形状和不同材料类型或成分可控分布的多材料结构。增材制造(AM)可以基于逐层原理提供高设计自由度和制造复杂零件的灵活性,能够精确控制材料的空间分布,因此在多材料结构的设计和制造中具有很大的潜力。与传统制造技术相比,多材料加工技术为几何形状复杂的多材料零件的制造提供了一种更加可靠的方法,降低了制造成本。特别是,这一过程引入了更高层次的设计自由,能够控制复杂的三维空间内材料分布的方向性和多样性。因此,多材料AM可以实现“在正确的位置打印正确的材料”和“为独特的功能打印独特的结构”。
与成品零件质量相关的要求包括满足标准化机械性能要求、表面粗糙度标准和精度。这些特性受到激光辐射引起的熔化和凝固现象的影响。因此,熔化和凝固过程中出现的内部缺陷和表面粗糙度不一致被认为会影响成品零件的质量。工艺参数对内部缺陷和/或成品密度的影响经常被报道。因此,激光功率、扫描速度、阴影间距和层厚度被确定为LB-PBF-LB工艺参数的基本参数。激光功率和扫描速度过程图用于确定最佳过程参数。
在金属增材制造工艺中,粉末床熔融(PBF)是经济影响最大的工艺,也是许多研究的主题。两种最常见的PBF工艺是激光PBF(LPBF)和电子束PBF(EBPBF)。LPBF,也称为选择性激光熔化,是在惰性气体环境中将激光光栅化在细粉床表面,导致选定区域熔化和融合的过程。通过铺设和融合连续层可以形成复杂的三维零件。EBPBF基于与LPBF相同的原理,但源是电子束而不是激光,并且腔室处于真空状态。对于EBPBF,每一层都由散焦光束烧结,以防止烟雾并实现接近完全致密的零件。1,2LPBF和EBPBF是用于制造本研究所用样品的过程。
Ti-6Al-4V具有良好的强度重量比,高抗疲劳和耐腐蚀性以及高温性能,导致许多航空航天应用。31Ti-6Al-4V还具有生物相容性,使其成为生物医学应用的理想选择。与其他合金相比,Al-Si-10Mg还具有良好的强度,耐腐蚀性,低密度和高导热性,并且经常出现在航空航天和汽车部件以及功能原型中。
本研究旨在研究LB-PBF零件的表面纹理与内部缺陷或密度之间的相关性,从而为开发能够防止LB-PBF零件缺陷发生的现场监测和反馈控制系统提供指导。
结果和讨论
工艺参数与密度的关系
本研究中进行的实验包括制作尺寸为10 × 10 × 10 mm(图1A)。使用配备有1kW单模光纤激光器的PBF测试台进行样品制造,在氮气环境(氧气含量 < 0.1重量%)。制造过程中考虑的其他操作条件包括激光光斑直径d = 100μm(1/e2),激光功率P = 175–800 W,扫描速度v = 550–2850 mm/s,阴影间距h = 0.10 mm,层厚t = 0.05mm,能量密度E = 24.1–82.4 J/mm3。能量密度E使用关系式E=\frac{P}{vht}计算。因此,在宽范围的激光功率(高达800 W)和扫描速度(高达2850 mm/s)值上研究了工艺参数和密度之间的关系。
使用本研究中制造的120个立方样品的相对密度值评估的激光功率与扫描速度的过程图如图1B所示。通过将竣工样品的基于阿基米德原理的密度除以其相应的真实密度(8.20 g/cm3)来计算相对密度。图1B中的低功率和低扫描速度区域对应于超过99.7%的高相对密度值。同时,以高功率(超过400W)和高扫描速度(超过2000mm/s)为特征的区域代表低相对密度。
使用材料和表面形貌特征变化相当大的金属AM样品进行实验,并选择测量参数以揭示最先进的CSI系统性能的最重要和最有趣的方面。可以使用收益递减的其他样本和测量参数进行进一步的研究,但作者的实验有限,以尽量减少冗余并保持简洁。实验包括(1)五个常见的金属增材制造表面,涵盖大范围的表面粗糙度、斜率分布和特征地形,以及(2)使用四个物镜和两个光学变焦设置、两个光谱滤光片、五个信号过采样设置和两个 HDR 照明水平的组合进行的一系列测量。对于每个表面,建议在数据覆盖范围、测量区域和时间方面进行优化测量。
图2描绘了高密度和低密度立方体样品的扫描电子显微镜(SEM)和X射线计算机断层扫描(XCT)图像;分别使用JEOL JSM-7800F和Nikon XT H225ST捕获这些图像。使用43.5 J/mm3的足够能量密度制造的全密度样品(XCT-1)的SEM和XCT图像显示,直径小于10μm的微孔很少(图2A、C、E)。同时,在29J/mm3的低能量密度下制造的相对密度为98%的样品(XCT-2)的SEM和XCT图像显示了大量大量的未熔合缺陷(图2B、D、F)。
因此,在2000 mm/s扫描速度和超过35 J/mm3的能量密度下,可以在消耗小于500 W激光功率的情况下制造出接近真实密度的样品。此外,相对密度超过99.7%的样品的结构特征在于存在小于 ~ 直径为10μm(图2G)。这不会显著影响LB-PBF IN718的疲劳强度。因此,将99.7%的相对密度设置为阈值。
试样S1–S9(参见图1B,C)的光学显微镜(OM)图像如图3所示。如图所示,全密度试样S7、S8和S9中存在极少的缺陷。同时,相对密度为99%的试样S4中存在少量孔隙,而相对密度较低的试样S1、S2和S3中可观察到没有熔合缺陷和孔隙。根据20,相对密度值低于约99%的材料中容易出现熔合缺陷。因此,随着材料相对密度的降低,这些缺陷变得更加突出。
AM表面具有高粗糙度,并包含大量高斜率和松散颗粒。因此,很难以高分辨率准确测量表面形貌。CSI技术最初设计用于测量相对光滑的表面(例如光学器件)。这种技术以前被认为不适用于测量AM表面;然而,CSI技术开发的最新进展允许通过使用先进的测量功能显着提高检测灵敏度,例如源光谱的过滤,HDR照明水平,每个干涉条纹上的可调相机采集数量以及复杂的地形重建算法。
在金属增材制造技术的实施过程中,现场监控和反馈控制系统的可用性确保了高质量的成品零件的制造。本研究旨在研究激光束粉末床熔合(LB-PBF)零件的表面纹理与内部缺陷或密度之间的相关性。在本研究中,通过将LB-PBF工艺应用于In 718镍合金粉末,制备了120个立方试样。根据ISO 25178–2标准,确定了制造样品的密度和35个表面纹理参数。使用统计方法,观察到区域表面纹理参数与试样内的密度或内部缺陷之间存在很强的相关性。对这些区域表面纹理参数的现场监测可以有助于将其用作反馈系统中的控制变量。
介绍
金属增材制造(AM),尤其是粉末床熔合(PBF),被认为是创造具有精致材料性能和复杂结构的新材料的重要过程。该工艺涉及使用激光或电子束作为热源。然而,人们对使用PBF工艺获得的成品零件的质量提出了一些担忧。这些问题涉及到成品零件中出现气孔和未熔合等缺陷,以及由于PBF工艺固有的特性导致加工过程中表面粗糙度的增加。因此,发现PBF制造零件的机械性能和表面粗糙度低于锻造材料。因此,为了尽量减少PBF加工过程中缺陷的发生并确保成品零件的高质量,开发了监控和反馈控制系统。
使用传统的制造技术,如粉末冶金、轧制、焊接、化学气相沉积和扩散连接,很难制造具有复杂几何形状和不同材料类型或成分可控分布的多材料结构。增材制造(AM)可以基于逐层原理提供高设计自由度和制造复杂零件的灵活性,能够精确控制材料的空间分布,因此在多材料结构的设计和制造中具有很大的潜力。与传统制造技术相比,多材料加工技术为几何形状复杂的多材料零件的制造提供了一种更加可靠的方法,降低了制造成本。特别是,这一过程引入了更高层次的设计自由,能够控制复杂的三维空间内材料分布的方向性和多样性。因此,多材料AM可以实现“在正确的位置打印正确的材料”和“为独特的功能打印独特的结构”。
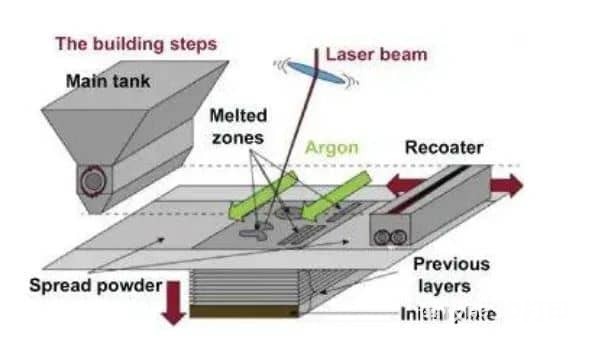
标准L-PBF系统的示意图。
与成品零件质量相关的要求包括满足标准化机械性能要求、表面粗糙度标准和精度。这些特性受到激光辐射引起的熔化和凝固现象的影响。因此,熔化和凝固过程中出现的内部缺陷和表面粗糙度不一致被认为会影响成品零件的质量。工艺参数对内部缺陷和/或成品密度的影响经常被报道。因此,激光功率、扫描速度、阴影间距和层厚度被确定为LB-PBF-LB工艺参数的基本参数。激光功率和扫描速度过程图用于确定最佳过程参数。
在金属增材制造工艺中,粉末床熔融(PBF)是经济影响最大的工艺,也是许多研究的主题。两种最常见的PBF工艺是激光PBF(LPBF)和电子束PBF(EBPBF)。LPBF,也称为选择性激光熔化,是在惰性气体环境中将激光光栅化在细粉床表面,导致选定区域熔化和融合的过程。通过铺设和融合连续层可以形成复杂的三维零件。EBPBF基于与LPBF相同的原理,但源是电子束而不是激光,并且腔室处于真空状态。对于EBPBF,每一层都由散焦光束烧结,以防止烟雾并实现接近完全致密的零件。1,2LPBF和EBPBF是用于制造本研究所用样品的过程。
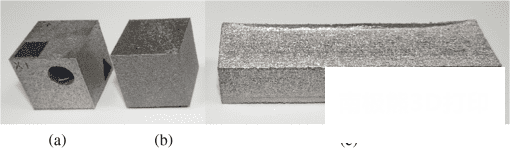
样品图片:(a)Al-Si-10Mg,(b)Ti-6Al-4V LPBF立方体和(c)Ti-6Al-4V EBPBF矩形棱镜。
Ti-6Al-4V具有良好的强度重量比,高抗疲劳和耐腐蚀性以及高温性能,导致许多航空航天应用。31Ti-6Al-4V还具有生物相容性,使其成为生物医学应用的理想选择。与其他合金相比,Al-Si-10Mg还具有良好的强度,耐腐蚀性,低密度和高导热性,并且经常出现在航空航天和汽车部件以及功能原型中。
本研究旨在研究LB-PBF零件的表面纹理与内部缺陷或密度之间的相关性,从而为开发能够防止LB-PBF零件缺陷发生的现场监测和反馈控制系统提供指导。
结果和讨论
工艺参数与密度的关系
本研究中进行的实验包括制作尺寸为10 × 10 × 10 mm(图1A)。使用配备有1kW单模光纤激光器的PBF测试台进行样品制造,在氮气环境(氧气含量 < 0.1重量%)。制造过程中考虑的其他操作条件包括激光光斑直径d = 100μm(1/e2),激光功率P = 175–800 W,扫描速度v = 550–2850 mm/s,阴影间距h = 0.10 mm,层厚t = 0.05mm,能量密度E = 24.1–82.4 J/mm3。能量密度E使用关系式E=\frac{P}{vht}计算。因此,在宽范围的激光功率(高达800 W)和扫描速度(高达2850 mm/s)值上研究了工艺参数和密度之间的关系。
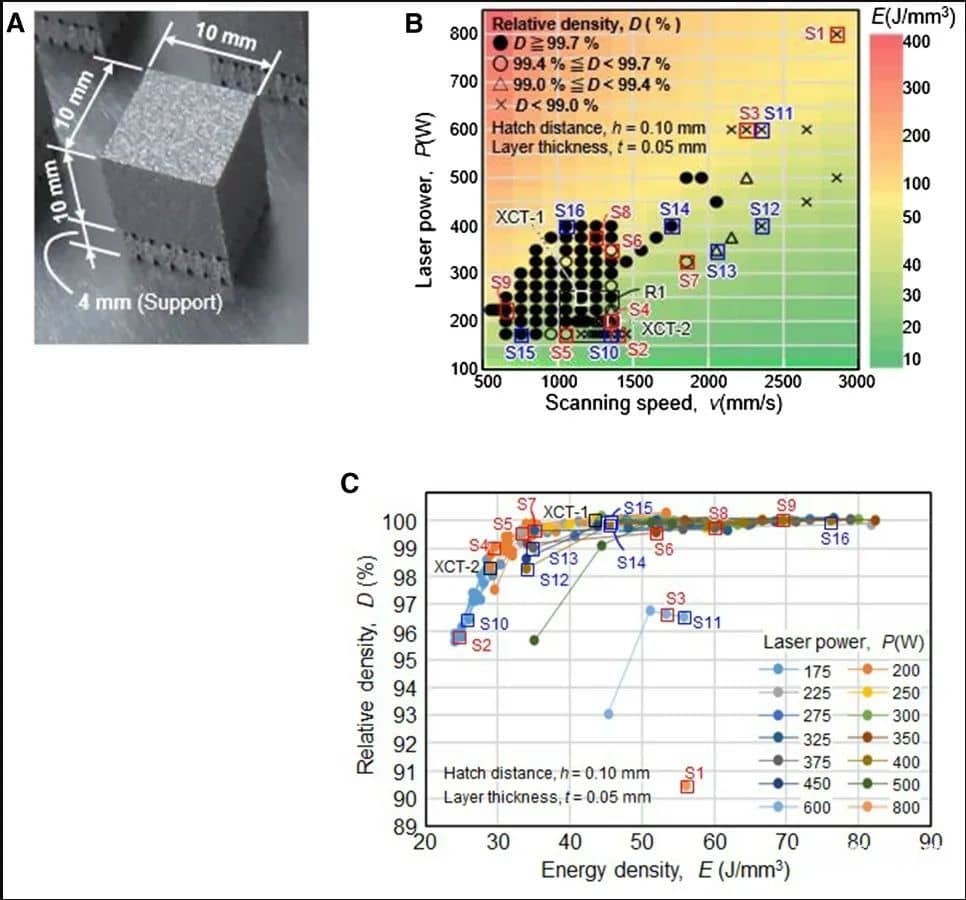
图1 通过工艺参数和密度之间的相对密度评估的关系,(A)立方试样;(B)激光功率和扫描速度之间的过程图;(C)相对密度和能量密度之间的关系。
使用本研究中制造的120个立方样品的相对密度值评估的激光功率与扫描速度的过程图如图1B所示。通过将竣工样品的基于阿基米德原理的密度除以其相应的真实密度(8.20 g/cm3)来计算相对密度。图1B中的低功率和低扫描速度区域对应于超过99.7%的高相对密度值。同时,以高功率(超过400W)和高扫描速度(超过2000mm/s)为特征的区域代表低相对密度。
使用材料和表面形貌特征变化相当大的金属AM样品进行实验,并选择测量参数以揭示最先进的CSI系统性能的最重要和最有趣的方面。可以使用收益递减的其他样本和测量参数进行进一步的研究,但作者的实验有限,以尽量减少冗余并保持简洁。实验包括(1)五个常见的金属增材制造表面,涵盖大范围的表面粗糙度、斜率分布和特征地形,以及(2)使用四个物镜和两个光学变焦设置、两个光谱滤光片、五个信号过采样设置和两个 HDR 照明水平的组合进行的一系列测量。对于每个表面,建议在数据覆盖范围、测量区域和时间方面进行优化测量。
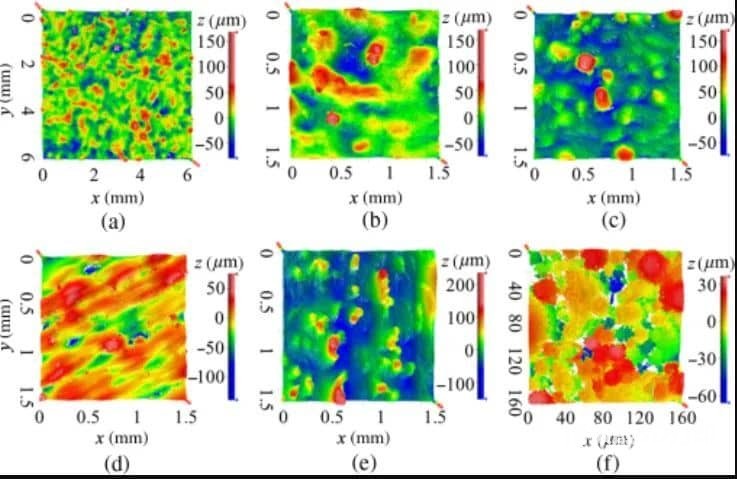
金属增材制造表面的CSI测量。
图2描绘了高密度和低密度立方体样品的扫描电子显微镜(SEM)和X射线计算机断层扫描(XCT)图像;分别使用JEOL JSM-7800F和Nikon XT H225ST捕获这些图像。使用43.5 J/mm3的足够能量密度制造的全密度样品(XCT-1)的SEM和XCT图像显示,直径小于10μm的微孔很少(图2A、C、E)。同时,在29J/mm3的低能量密度下制造的相对密度为98%的样品(XCT-2)的SEM和XCT图像显示了大量大量的未熔合缺陷(图2B、D、F)。
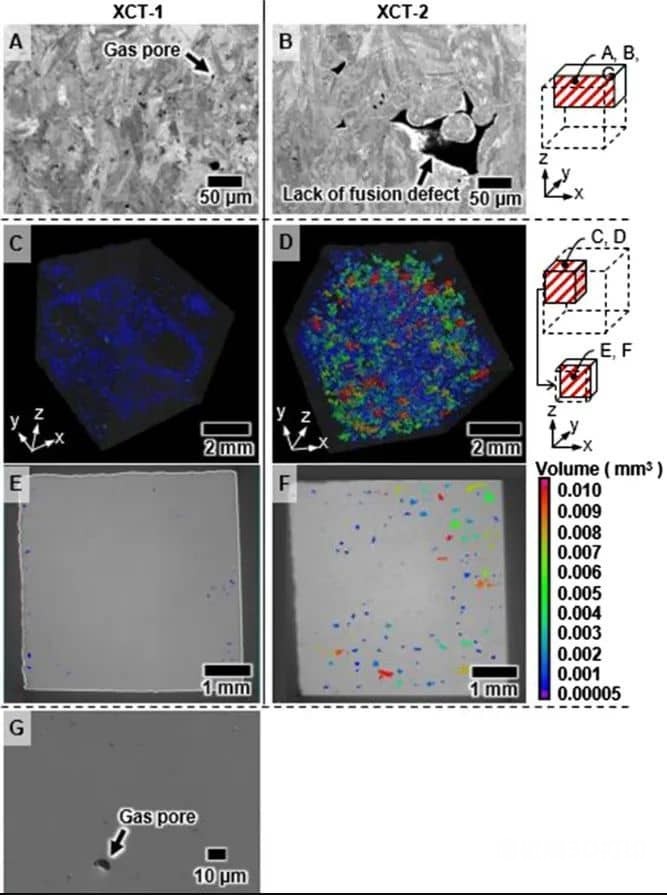
图2 立方试件内部缺陷的观察。
因此,在2000 mm/s扫描速度和超过35 J/mm3的能量密度下,可以在消耗小于500 W激光功率的情况下制造出接近真实密度的样品。此外,相对密度超过99.7%的样品的结构特征在于存在小于 ~ 直径为10μm(图2G)。这不会显著影响LB-PBF IN718的疲劳强度。因此,将99.7%的相对密度设置为阈值。
试样S1–S9(参见图1B,C)的光学显微镜(OM)图像如图3所示。如图所示,全密度试样S7、S8和S9中存在极少的缺陷。同时,相对密度为99%的试样S4中存在少量孔隙,而相对密度较低的试样S1、S2和S3中可观察到没有熔合缺陷和孔隙。根据20,相对密度值低于约99%的材料中容易出现熔合缺陷。因此,随着材料相对密度的降低,这些缺陷变得更加突出。
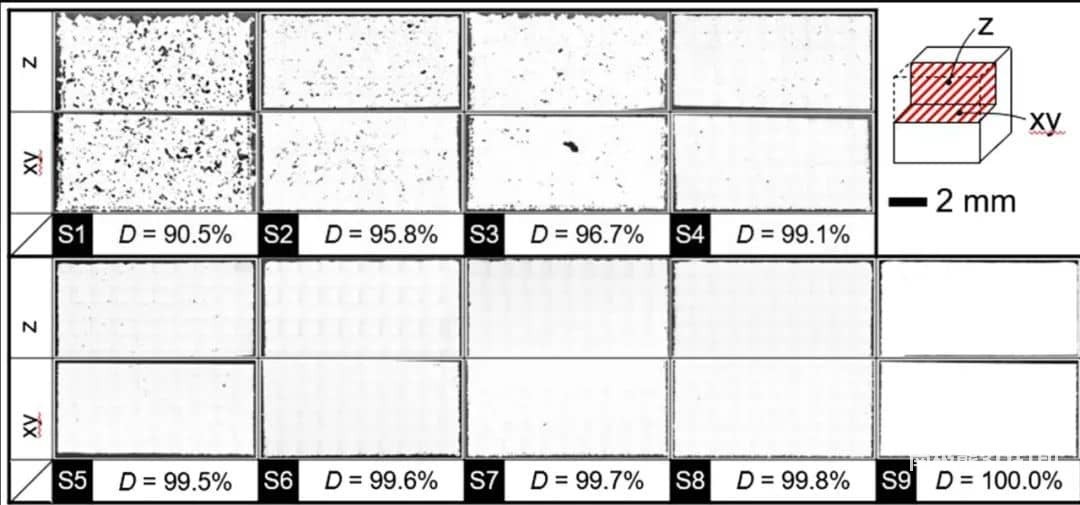
图3 试样(S1–S9)横截面的OM图像。
AM表面具有高粗糙度,并包含大量高斜率和松散颗粒。因此,很难以高分辨率准确测量表面形貌。CSI技术最初设计用于测量相对光滑的表面(例如光学器件)。这种技术以前被认为不适用于测量AM表面;然而,CSI技术开发的最新进展允许通过使用先进的测量功能显着提高检测灵敏度,例如源光谱的过滤,HDR照明水平,每个干涉条纹上的可调相机采集数量以及复杂的地形重建算法。
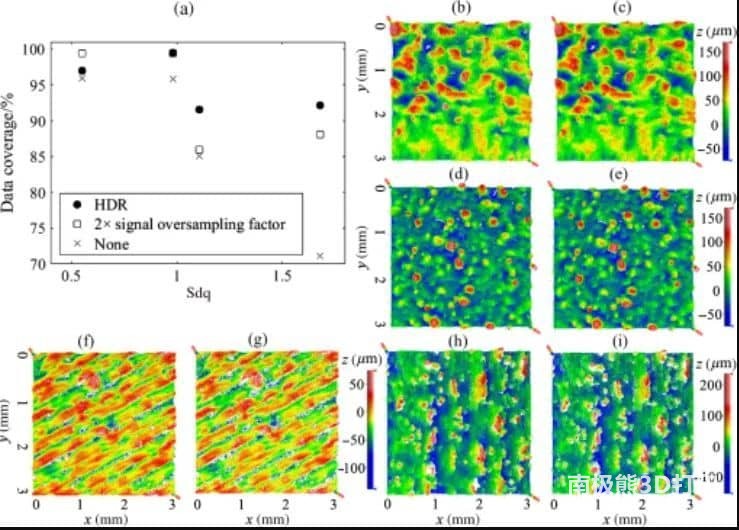
为照明水平启用HDR功能可以增强数据覆盖范围。
(责任编辑:admin)
最新内容
热点内容