综述:金属增材制造—微观结构演变与多阶段控制(一)(2)
时间:2021-08-17 11:54 来源:南极熊 作者:admin 阅读:次
将能量和几何术语整合到新的加工图中,大致可以分为四个区域:I. 缺乏结合,II. 缺乏熔合,II. 流程窗口和 IV. 钥孔形成。通过在工艺窗口区域(III) 中完全熔化和充分结合稳定的熔池,可以建造致密的金属部件。由于能量输入不足,熔池温度低,流动性弱,出现球化现象。即使当能量密度足够高以熔化连续轨道时,由大舱口间距或大层厚度引起的小重叠仍然会导致缺乏结合缺陷。根据综合加工图,能源只是提供稳定熔池的前提;熔池的几何重叠是构建致密金属部件的另一个必要条件。请注意,加工图的四个区域之间的边界是通过简单的物理推理提出的;实际上,它们应该被视为不确定区域,而不是尖锐的边界。基于这张增材制造的综合加工图,最佳工艺窗口从VED的最大密度点显着扩展到二维区域,并且可以克服VED的局限性。由几何重叠引起的复杂热历史自然发生在横坐标上,并且可以通过调整增材制造过程中的重叠度来轻松定制本征热处理。
在之前的研究中,一些研究人员采用熔池几何形状来预测增材制造的打印质量。唐等人,提出了由相对舱口间距(h/d)和相对层厚度(δ/w)构建的加工图来预测未熔合孔隙度,其中d表示熔池深度,等于熔池宽度的一半。对于足够的熔池重叠,横向相邻熔池之间的重叠深度 l* 不得大于用于零件打印的层厚度。巴贾吉等人,采用归一化舱口间距rb/h作为几何因子,结合归一化能量构建归一化加工图。他们还确定了一个宽的工艺窗口,具有能量输入和熔池重叠的中间值,以实现最小的孔隙率。此外,新的综合加工图可以在打印前提供有关打印微观结构的信息。托马斯等人,发现大重叠和能量输入的组合导致由 EBM 制造的 Ti-6Al-V 合金中相对粗糙的 β 结构。这些发现表明,通过在基于能量几何的加工图中仔细选择工艺参数,可以控制孔隙率和微观结构。
从综合加工图中,可以明显看出金属部件增材制造的两个基本物理步骤:单个熔池的形成和随后多个熔池的结合。这些步骤建立了制造的基本热历史,从而通过增材制造过程中的凝固和循环热效应确定印刷金属的最终微观结构。沿着这个思路,金属材料的增材制造微观结构可以看作是在不同制造阶段形成的结构,即凝固和凝固后的微观结构。
3. 凝固微观结构
原则上,增材制造微观结构的主要部分是由熔池凝固阶段的晶粒成核和生长形成的。众所周知,凝固过程中热量和溶质的传递在决定最终晶粒尺寸和形态方面起着主导作用。高度聚焦的光束和大的扫描速度使熔池具有较小的尺寸,从而导致具有陡峭温度梯度和快速凝固速度的凝固条件。因此,打印金属材料的显著微观结构特征是由熔池边界的晶体外延生长形成的柱状晶粒。这些柱状晶粒的直径通常为几微米到几十微米,如图3(a)所示。由于柱状晶是在初始凝固阶段形成的,可以看作是初级凝固结构。此外,尽管在增材制造过程中通过快速冷却抑制了微观偏析,但在某些情况下,溶质重新分布仍然可以发挥作用。二级相可以在柱状晶粒之间的枝晶间区域沉淀,例如在通过增材制造制造的铝和镍合金中。这些富含溶质的沉淀物可视为二次凝固结构,如图3(b)所示。初级柱状颗粒和二次沉淀物主要受输入能量的影响,即图2(b)综合加工图中的能量项。只有当熔化发生时,凝固微观结构才会打印到金属上,如图3(e)中复杂的热历史所示。
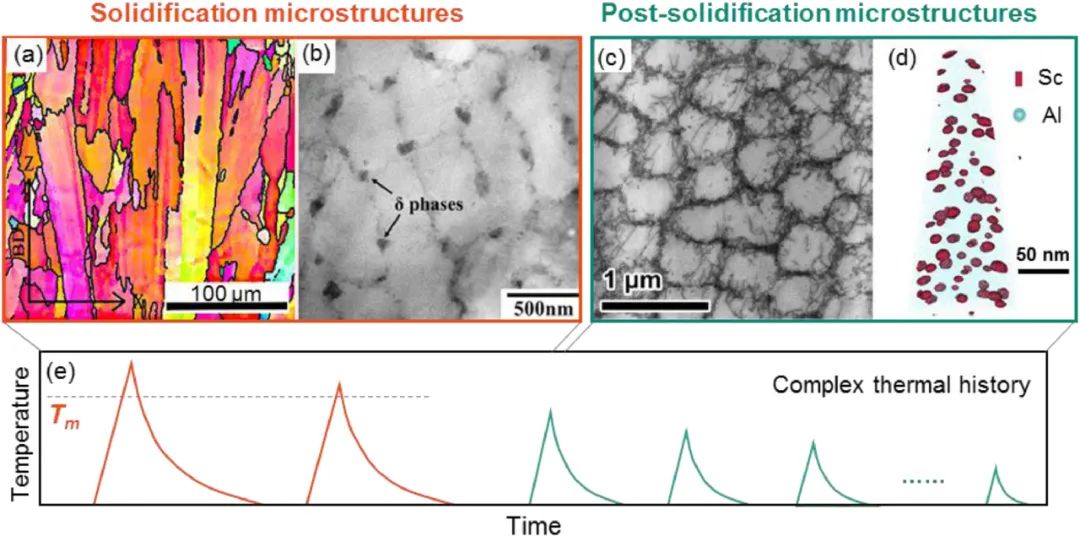
▲图3 通过增材制造制造的金属的微观结构演变。凝固结构包括(a)初级柱状晶粒和(b)沿柱状晶界稀疏分布的次级相。固化后结构包括(c)位错单元和(d)基质中的纳米沉淀物。(e)复杂的热历史有助于在增材制造过程中形成多级微观结构。
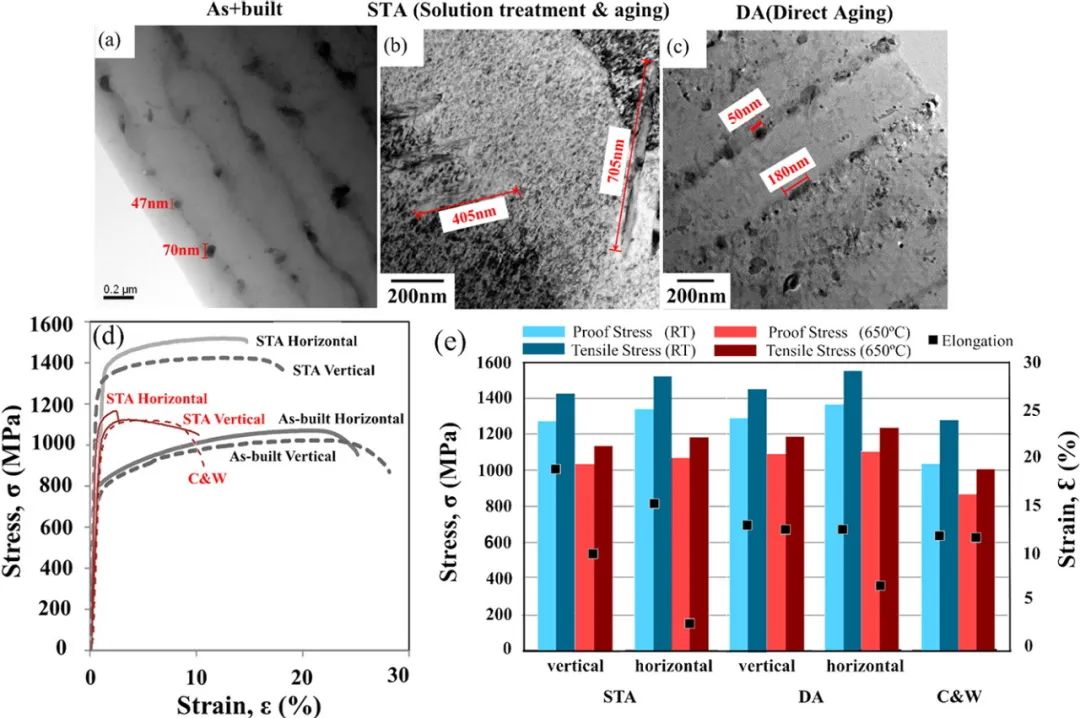
▲图3-1 在每一718 高温合金样品进行增材制造时,高温合金718的δ相在枝晶间区域析出 ((a), (b), (c)),样品的沉积态和热处理之后同铸造状态和变形状态样品的拉伸强度的对比(d),然而,平行的样品呈现出的韧性同垂直的样品相比较,在 650 °C的时候只有四分之一(e);同时发现,未期待的枝晶间 δ相将会提供在拉伸测试时初始的裂纹萌生源和扩展源
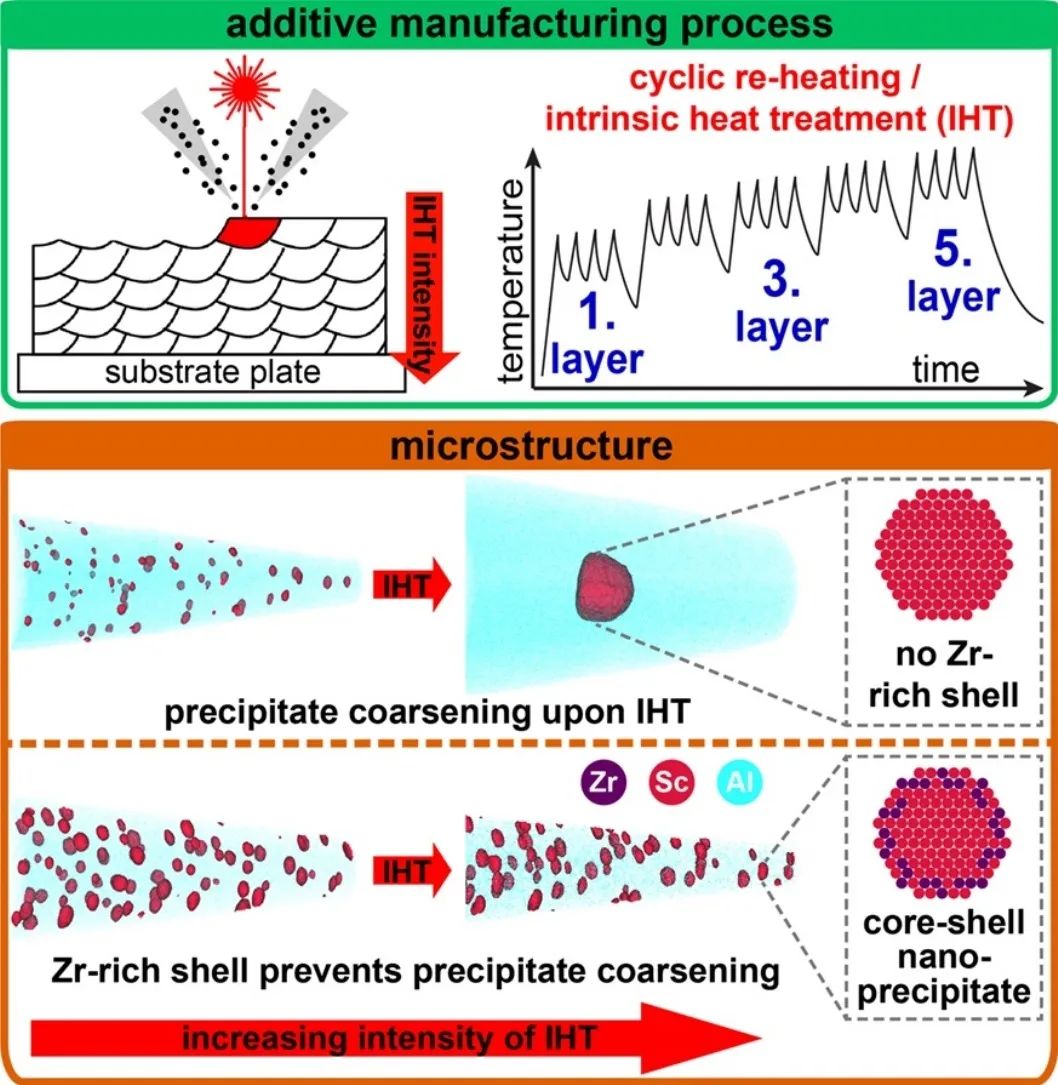
▲图3-2增材制造铝合金Al-Sc-Zr时热稳定的芯壳纳米析出相的控制
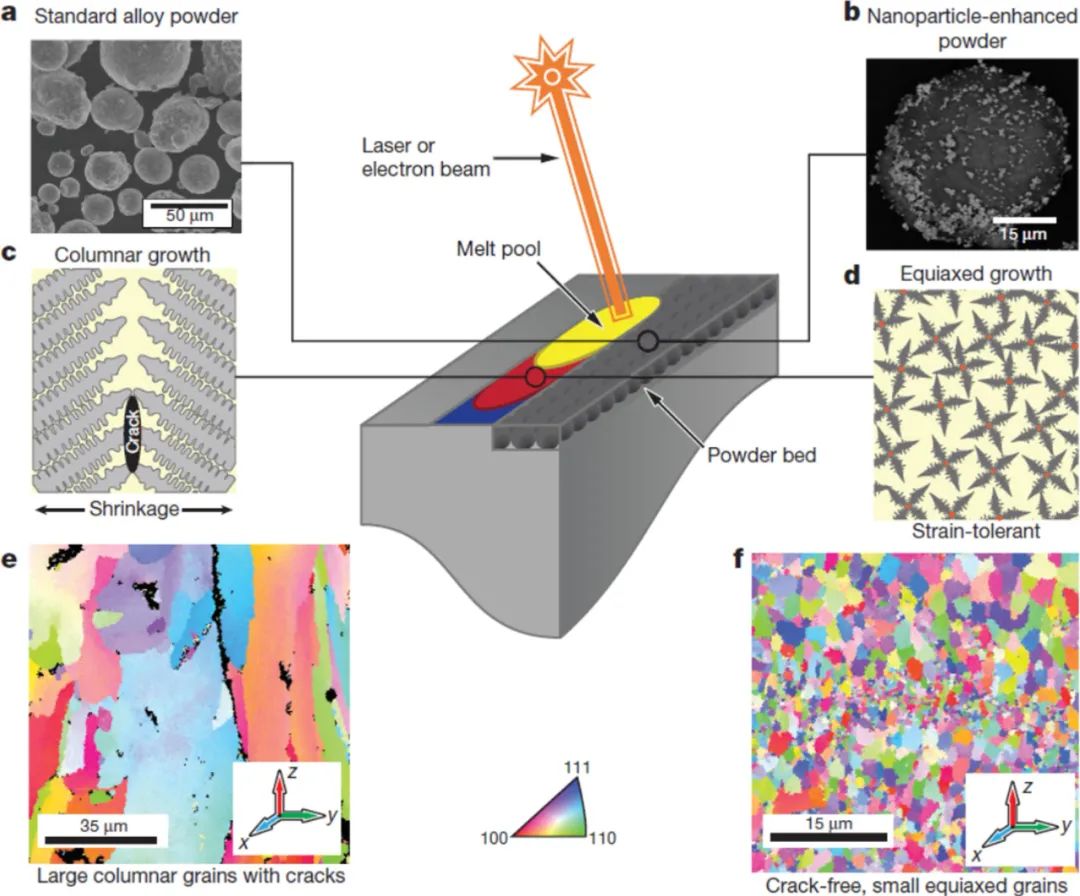
▲图3-3 添加晶格匹配的纳米颗粒到高强Al合金中来代替细长的等轴晶和避免产生裂纹
3.1 微尺度的初生柱状结构
基于经典凝固理论,对于给定合金,初级晶粒的微观结构主要由熔池中的局部凝固条件决定,包括温度梯度G和凝固速率V。G/V系数控制这凝固模式,其产物冷却速率控制着凝固微观结构的规模。如图4(a)所示,随着热量被传热到固体基底上,凝固从先前沉积的基底定向进行到熔融液体。异相成核存在可忽略的成核障碍;因此,晶粒生长现象决定了大部分最终的微观结构。在晶粒生长过程中,溶质原子被排斥到液体中并在固液界面前形成溶质积累层(图4(b)),根据图4(c)中的相图,这会扩大冻结范围。因此,由于微观偏析(图4(d)),会出现结构过冷。生长过程中固液界面的结构过冷和形态稳定性共同作用,对最终的快速凝固微观结构产生很大影响。
3.1.1 初级柱状颗粒的大小
在增材制造过程中,金属粉末的局部加热会导致熔池中心的峰值温度很高;因此,在熔池边界附近形成了一个陡峭的温度梯度。由于功率的热扩散系数远低于相应的固体材料,因此熔体内的热量主要通过先前构建的层消散,从而导致制造方向上的温度梯度。此外,当高能光束扫过时,小熔池中的凝固立即开始。由于陡峭的温度梯度和高凝固速率,预计柱状晶粒在增材制造的微观结构中占主导地位,如图4(e)所示。柱状晶粒的特征尺寸,即柱状间距,根据凝固条件的不同而不同。与传统铸造相比,亚稳态微观结构表明增材制造过程中存在非平衡凝固过程,其中热场除扩散场外也起着重要作用。在这种情况下,枝晶尖端形态可能发生变化,应考虑液固界面稳定性标准。基于测试良好的 Kurz-Fisher模型,表明晶粒尺寸与凝固速率、温度梯度和冷却速率成反比。在高能束快速扫描过程中,凝固速率V通过扫描方向与熔池边界的倾角θ与扫描速度有关,V= v·cosθ。增材制造的扫描速度通常大于10exp(-1) m/s,所以,快速凝固条件在制造过程中占主导地位。因此,通过增材制造制造完全等轴晶粒具有挑战性。
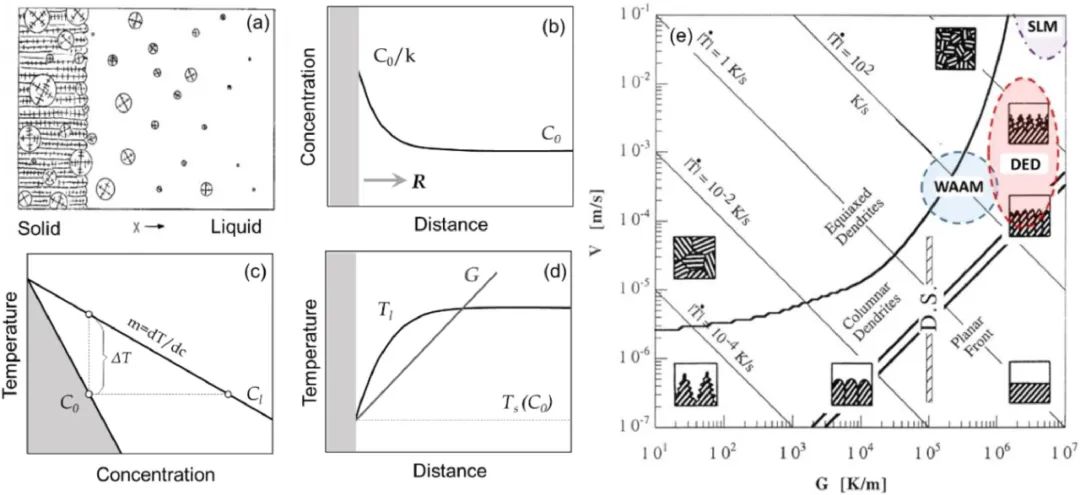
▲图4 (a)快速凝固过程中固液界面柱状和等轴晶粒生长示意图。(b)由于溶质在液体和固体中的溶解度不同,导致固液界面前的溶质分离。(c)典型相图的一部分,表示结构过冷。(d)固液界面前端溶质偏析引起的结构过冷。(e)表示增材制造的柱状到等轴转换的示意图。
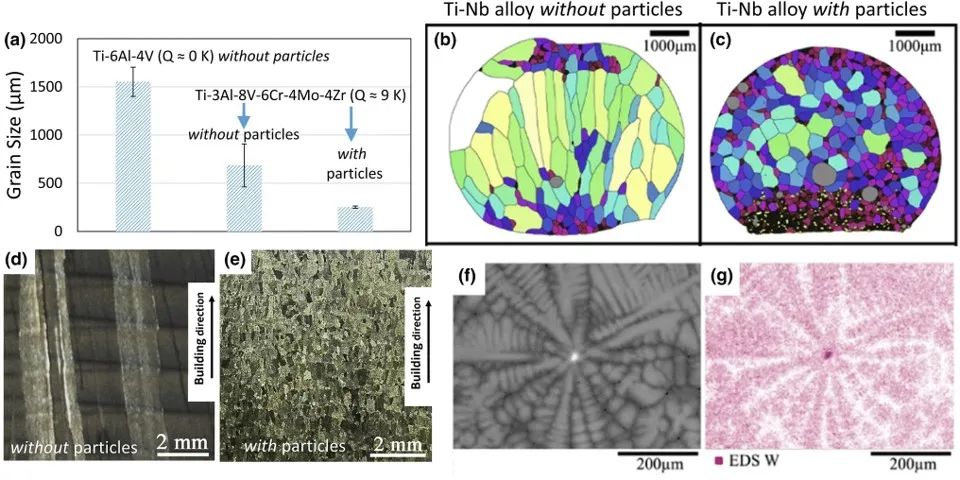
▲图4-1孕育颗粒对不同钛合金的晶粒形成的影响
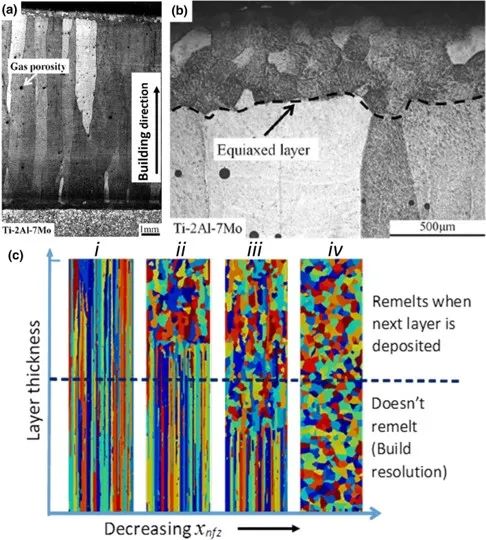
▲图4-2 柱状晶向等轴晶的过渡转变也许会发生G和V的变化时在层层之间发生。最有利于等轴晶的最优凝固状态发生在每一层的最上方。这一研究是Zheng等人在LMD工艺制造Ti-2Al-7Mo合金的时候观察到的CET。
大量研究表明,增材制造金属的柱状微观结构主要受熔池实时热场的控制,而熔池的实时热场受增材制造过程中激光功率和扫描速度的影响。由于复杂的热条件,工艺参数和凝固因素之间的定量关系仍然不存在。使用分析模型揭示了一些一般趋势。例如,由于熔池的液体寿命较短和单位时间的能量输入较低,凝固和冷却速率随着扫描速度的增加而增加。对于恒定的扫描速度,由于熔池的峰值温度较低和液体寿命显着延长,温度梯度减小,冷却速率随着激光功率的降低而增加。基于这些发现,已经进行了一些研究来调整柱状晶粒的大小。例如,Spierings等人,发现扫描速度的增加导致晶粒尺寸分布向更小的晶粒移动,这是在高扫描速度下获得更高冷却速率的结果。Wang等人,表明由于较高的温度和熔池过冷程度的降低,平均初级枝晶间距随着扫描速度的降低而增加。Priya等人,证明较高的激光功率和较低的扫描速度会导致更粗糙的微观结构,这归因于整个熔池深度的凝固时间变化较小;这意味着熔池中的冷却速度较低。对于不同的增材制造技术,典型的冷却速度有所不同;SLM大约为10exp(6)K/s,高于LENS(10exp(5)K/s)、EBM(10exp(4)K/s)和WAAM(10exp(2)K/s)。因此,SLM可以在最终的金属元件中产生更精细的微观结构,如图4(e)所示。
(责任编辑:admin)
最新内容
热点内容