粉末基增材制造金属和合金过程的多尺度缺陷的形成原因及修正方法
时间:2024-01-16 09:30 来源:航空燃机资讯 作者:admin 阅读:次
由于增材制造(AM)技术提供了出色的设计自由度,具有复杂几何形状的部件可以基于预定义的计算机辅助设计(CAD)模型轻松地逐层制造。各种 AM 技术已经被开发并广泛应用于设计和制造用于关键工业应用的高性能组件,包括航空航天,医疗和汽车领域。
基于粉末的增材制造金属和合金中多尺度缺陷的类型包括尺寸缺陷、表面质量缺陷、显微组织缺陷以及成分缺陷。香港理工大学、西北工业大学和香港中文大学的傅铭旺教授等人提出了基于粉末的增材制造金属和合金过程中的多尺度缺陷,并阐明了各类缺陷形成的潜在机制以及控制方法;总结了金属增材制造各类缺陷的破坏性和非破坏性检测方法;介绍了多尺度增材制造缺陷建模的研究进展;分析讨论了各类缺陷对增材制造件的拉伸及疲劳力学性能的影响机制。
多尺度缺陷的分类概览
金属 AM 部件的性能在很大程度上取 决于其表面质量和微观结构特征。影响表面质量和微结构的主要因素包括材料性能、设计相关因素、工艺参数和系统设置。不适当的工艺配置可能会在最终的 AMed 组件中引入缺陷,例如孔隙和裂纹。基于现有的金属 AM 文献,在 AMed 金属零件和结构中识别出从毫米到纳米尺度的多尺度缺陷。如图所示,将多尺度缺陷主要分为三大类,即几何相关缺陷、表面完整性相关缺陷和微结构缺陷。特别地,我们首先将织构柱状晶粒,复合-结构缺陷和位错细胞在 AMed 件中普遍存在,并对 AMed 元件的性能产生重要影响。
1几何相关缺陷
几何缺陷主要来自于制造结构与理想 CAD 模型之间 的尺寸和几何偏差。几何相关缺陷主要包括零件变形和分层。分层是AM 过程中独特的开裂行为,这是由于 AM 的逐层制造模式的性质所决定的。典型的零件变形和分层如图 (a-c)]所示。零件变形和脱层是由宏观残余应力引起的,而宏观残余应力来源于空间热 梯度
例如,零件在热循环过程中的不均匀膨胀和收缩,以及不均匀的非弹性应变。影响残余应力相关变形的因素有很多。与设备相关的因素包括激光光斑尺寸、基板的厚度和预热等,都可能诱发这类缺陷。在我们宝贵的工作中,我们比较了微 LPBF(使用直径为 25 m 的细激光束)和常规 LPBF 产生的悬臂梁的畸变。如图 (a.d)所示,由于原位应力消除退火更显著,精细激光束产生的畸变更小。因此,微型 LPBF 系统更有可能生产出几何精度高的部件。此外,Corbin 等研究了衬底厚度和预热对 DED Ti6A14V 变形的影响。他们得出结论:衬底预热后,薄衬底的畸变有效降低,而厚衬底的畸变则增加。因此,选择合适的基板厚度和预热温度来减少残余应力是很重要的。
研究了激光功率、扫描速度、扫描层厚度和扫描策略等工艺参数对残余应力和零件变形的影响。Mugwagwa
等人报道了扫描速度和激光功率的增加导致由残余应力引起的 LPBFed
悬壁变形总体呈增加趋势,增加层厚会减少变形,但由于能量密度降低而增加孔隙率。Salem
等利用桥曲率法探讨了扫描策略对畸变的影响,结果表明,通过缩短扫描矢量,畸变幅度减小。相应地,Promoppatum 和 Yao报道,在
Ti6A14V的 SLM 中分别使用 5 mm 和 1 mm 的扫描长度时,残余应力从 185 MPa 降低到 90 MPa(图
(e))。工艺参数对残余应力影响的类似趋势也在中进行了回顾。
零件变形的设计相关因素包 括零件在基材上的方向和位置、零件形状、特征尺寸直接金属激光烧结 Ti6A14V 零件的几何精度。结果表明,几何误差随着特征尺寸的增加而减小并收敛到一个恒定值,表明尺寸相关收缩是几何不精度的原因。此外,悬空或突出特征在复杂结构中很常见,但由于缺乏底部支撑,它们难以通过 AM对于 PBF 工艺,粉末床可以作为这些结构的支撑。然而,由于粉末床与固体悬垂结构之间的电导率差异,可能会产生集中的残余应力,导致结构翘曲、卷曲和变形。因此,当构件具有悬垂或突出特征时,需要设计支撑结构。除了支撑悬垂特征外,良好的支撑结构设计还可以保证正确的热流流向基材,防止因高残余应力而产生较大的变形。
2表面完整性相关缺陷
表面完整性缺陷是指与 CAD 设计模型的理想轮廓相偏离的不均匀或不规则的表面特征。我们总结了造成 AMed 部件表面完整性相关缺陷的四个主要因素,即阶梯效应、部分熔化的粉末、球化效应和表面裂纹。与机械加工等传统制造工艺相比,这些缺陷导致表面粗糙度较高,质量和精度较低,这是 AM 工艺固有的局限性之一.
阶梯效应是指由于制造分辨率的限制,曲面和斜面的层层逐级通近。楼梯效应引起的平均表面粗糙度(Ra)由层厚度和相对于建筑方向的倾斜角(BD)决定。增加层厚会导致显著的楼梯效应和更大的表面粗糙度。对于 AM 的晶格结构,这种带有悬挑支柱的复杂几何形状很容易导致楼梯效应。alketan 等人利用 LPBF 制作了各种周期性金属胞状结构,发现由于表面胞状结构的倾斜角不断变化,因此与基于支柱的品格相比,表面胞状结构中的阶梯效应不那么明显,如图(a, b)所示。
影响 AMed 零件表面粗糙度的第二个因素是部分熔化的粉末当在 AM 过程中使用低能量输入时,粉末可以部分熔化并粘附在零件表面。由于部分熔化而产生的平均表面粗糙度可以达到与粒度相同的尺度。此外,与较小的粉末相比,较大尺寸的粉末更难完全熔化,从而导致较差的表面光洁度。不同的表面取向也导致了不同的表面粗糙度。在我们之前的工作中,我们报道了由于有更多的部分熔化的粉末,侧表面比顶表面具有更高的表面粗糙度,如图(c, d)所示。此外,众所周知,由于更多的粉末倾向于部分熔化并粘附在下表面,因此下表面通常比上表面具有更大的表面粗糙度。
在 AM 过程中,起球效应是一个相当普遍的问题,甚至被认为是金属 AM
中表面缺陷和气孔的主要原因之一,尤其是铝合金等轻质合金。它发生在 AM
过程中,因为液态金属的表面张力通过产生液体球体使表面积最小化。成球效应是一种复杂的冶金行为,它是由润湿性差和液滴飞溅引起的。如果能量输入不足,则熔池下部太浅,无法充分渗透到下部层,它不能克服上部的表面张力。这种较差的润湿性,直接导致液球的形成。
液球的形成。例如,在图 (e)中,随着激光扫描速度的增加(能量输入的减少),熔池被拉长。伴随着润湿性的降低,它往往会破裂成不连续的小球。在一定程度上增加能量输入,可以改善润湿性,抑制成球效应。然而,过多的能量输入可能会因液滴飞溅而再次诱发成球效应,如图 (f)所示。如此高的能量密度会产生不稳定的熔池,伴随着金属的蒸发和较大的反冲压力,致熔化的金属和未熔化的粉末飞溅。溅落的液态金属形成微尺度的凝固球体落在表面上。由于液体的低粘度和长寿命,这种液滴飞溅诱导的球化效应在高激光功率和低扫描速度的条件下普遍存在。而且,球化效应不仅会导致表面粗糙度增加,还会导致金属粉末沉积不均匀,并可能诱发孔隙和分层。
最后但并非最不重要的是,表面裂纹也是一个需要关注的关键缺陷。Tang 等在 SLM 制造 CM247LC 时采用边界扫描策略,旨在提高表面光洁度。虽然使用边界扫描策略获得了光滑的表面但结果表明,与体块区域相比,边界区域存在更多的裂纹,如图(g)所示。随后,作者检查了边界区和体区晶体结构,分别以粗柱状晶粒和细长织构晶粒为特征,如图 (h)所示。表面裂纹沿边界区域的高角度晶界出现。边界区较大的柱状晶粒与高密度的几何必要位错(GND)有关,这意味着更高的内应力,从而更高的裂纹敏感性。因此,在表面光洁度和表面附近区域的裂纹之间的权衡是裂纹敏感合金(如镍基高温合金)的 AM 的关键问题。需要同时考虑这些因素对工艺参数进行仔细优化。
基于粉末的增材制造金属和合金中多尺度缺陷的类型包括尺寸缺陷、表面质量缺陷、显微组织缺陷以及成分缺陷。香港理工大学、西北工业大学和香港中文大学的傅铭旺教授等人提出了基于粉末的增材制造金属和合金过程中的多尺度缺陷,并阐明了各类缺陷形成的潜在机制以及控制方法;总结了金属增材制造各类缺陷的破坏性和非破坏性检测方法;介绍了多尺度增材制造缺陷建模的研究进展;分析讨论了各类缺陷对增材制造件的拉伸及疲劳力学性能的影响机制。
多尺度缺陷的分类概览
金属 AM 部件的性能在很大程度上取 决于其表面质量和微观结构特征。影响表面质量和微结构的主要因素包括材料性能、设计相关因素、工艺参数和系统设置。不适当的工艺配置可能会在最终的 AMed 组件中引入缺陷,例如孔隙和裂纹。基于现有的金属 AM 文献,在 AMed 金属零件和结构中识别出从毫米到纳米尺度的多尺度缺陷。如图所示,将多尺度缺陷主要分为三大类,即几何相关缺陷、表面完整性相关缺陷和微结构缺陷。特别地,我们首先将织构柱状晶粒,复合-结构缺陷和位错细胞在 AMed 件中普遍存在,并对 AMed 元件的性能产生重要影响。
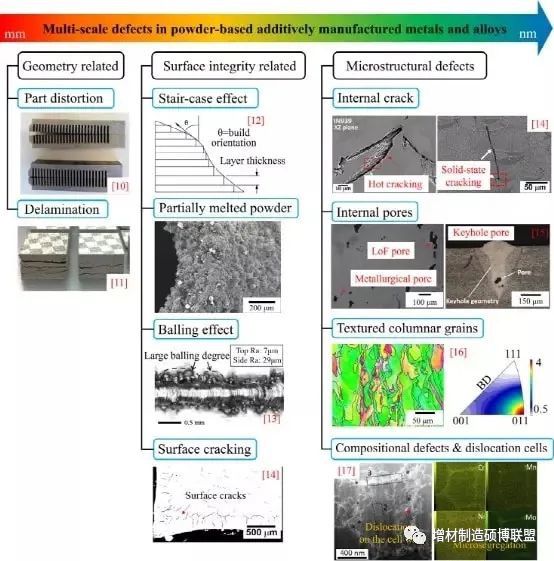
基于粉末的增材制造金属和合金中多尺度缺陷的分类
1几何相关缺陷
几何缺陷主要来自于制造结构与理想 CAD 模型之间 的尺寸和几何偏差。几何相关缺陷主要包括零件变形和分层。分层是AM 过程中独特的开裂行为,这是由于 AM 的逐层制造模式的性质所决定的。典型的零件变形和分层如图 (a-c)]所示。零件变形和脱层是由宏观残余应力引起的,而宏观残余应力来源于空间热 梯度
例如,零件在热循环过程中的不均匀膨胀和收缩,以及不均匀的非弹性应变。影响残余应力相关变形的因素有很多。与设备相关的因素包括激光光斑尺寸、基板的厚度和预热等,都可能诱发这类缺陷。在我们宝贵的工作中,我们比较了微 LPBF(使用直径为 25 m 的细激光束)和常规 LPBF 产生的悬臂梁的畸变。如图 (a.d)所示,由于原位应力消除退火更显著,精细激光束产生的畸变更小。因此,微型 LPBF 系统更有可能生产出几何精度高的部件。此外,Corbin 等研究了衬底厚度和预热对 DED Ti6A14V 变形的影响。他们得出结论:衬底预热后,薄衬底的畸变有效降低,而厚衬底的畸变则增加。因此,选择合适的基板厚度和预热温度来减少残余应力是很重要的。
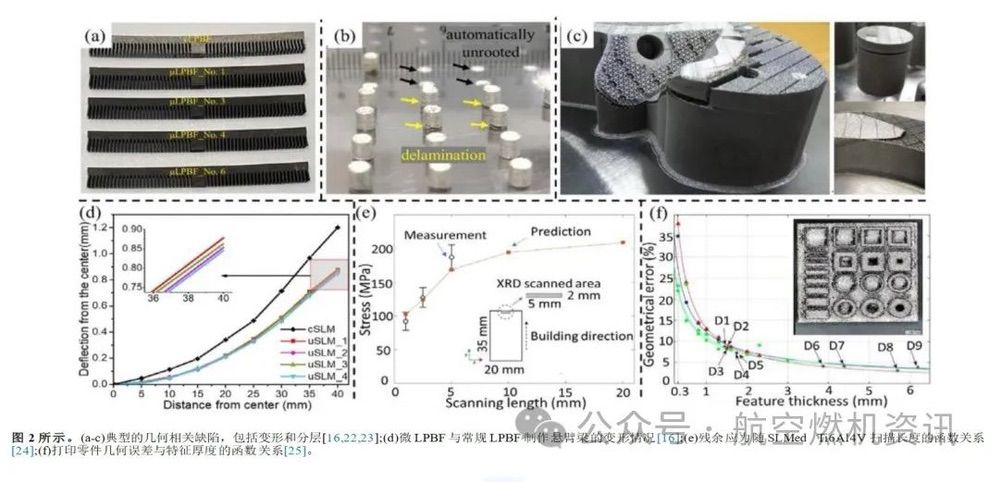
零件变形的设计相关因素包 括零件在基材上的方向和位置、零件形状、特征尺寸直接金属激光烧结 Ti6A14V 零件的几何精度。结果表明,几何误差随着特征尺寸的增加而减小并收敛到一个恒定值,表明尺寸相关收缩是几何不精度的原因。此外,悬空或突出特征在复杂结构中很常见,但由于缺乏底部支撑,它们难以通过 AM对于 PBF 工艺,粉末床可以作为这些结构的支撑。然而,由于粉末床与固体悬垂结构之间的电导率差异,可能会产生集中的残余应力,导致结构翘曲、卷曲和变形。因此,当构件具有悬垂或突出特征时,需要设计支撑结构。除了支撑悬垂特征外,良好的支撑结构设计还可以保证正确的热流流向基材,防止因高残余应力而产生较大的变形。
2表面完整性相关缺陷
表面完整性缺陷是指与 CAD 设计模型的理想轮廓相偏离的不均匀或不规则的表面特征。我们总结了造成 AMed 部件表面完整性相关缺陷的四个主要因素,即阶梯效应、部分熔化的粉末、球化效应和表面裂纹。与机械加工等传统制造工艺相比,这些缺陷导致表面粗糙度较高,质量和精度较低,这是 AM 工艺固有的局限性之一.
阶梯效应是指由于制造分辨率的限制,曲面和斜面的层层逐级通近。楼梯效应引起的平均表面粗糙度(Ra)由层厚度和相对于建筑方向的倾斜角(BD)决定。增加层厚会导致显著的楼梯效应和更大的表面粗糙度。对于 AM 的晶格结构,这种带有悬挑支柱的复杂几何形状很容易导致楼梯效应。alketan 等人利用 LPBF 制作了各种周期性金属胞状结构,发现由于表面胞状结构的倾斜角不断变化,因此与基于支柱的品格相比,表面胞状结构中的阶梯效应不那么明显,如图(a, b)所示。
影响 AMed 零件表面粗糙度的第二个因素是部分熔化的粉末当在 AM 过程中使用低能量输入时,粉末可以部分熔化并粘附在零件表面。由于部分熔化而产生的平均表面粗糙度可以达到与粒度相同的尺度。此外,与较小的粉末相比,较大尺寸的粉末更难完全熔化,从而导致较差的表面光洁度。不同的表面取向也导致了不同的表面粗糙度。在我们之前的工作中,我们报道了由于有更多的部分熔化的粉末,侧表面比顶表面具有更高的表面粗糙度,如图(c, d)所示。此外,众所周知,由于更多的粉末倾向于部分熔化并粘附在下表面,因此下表面通常比上表面具有更大的表面粗糙度。
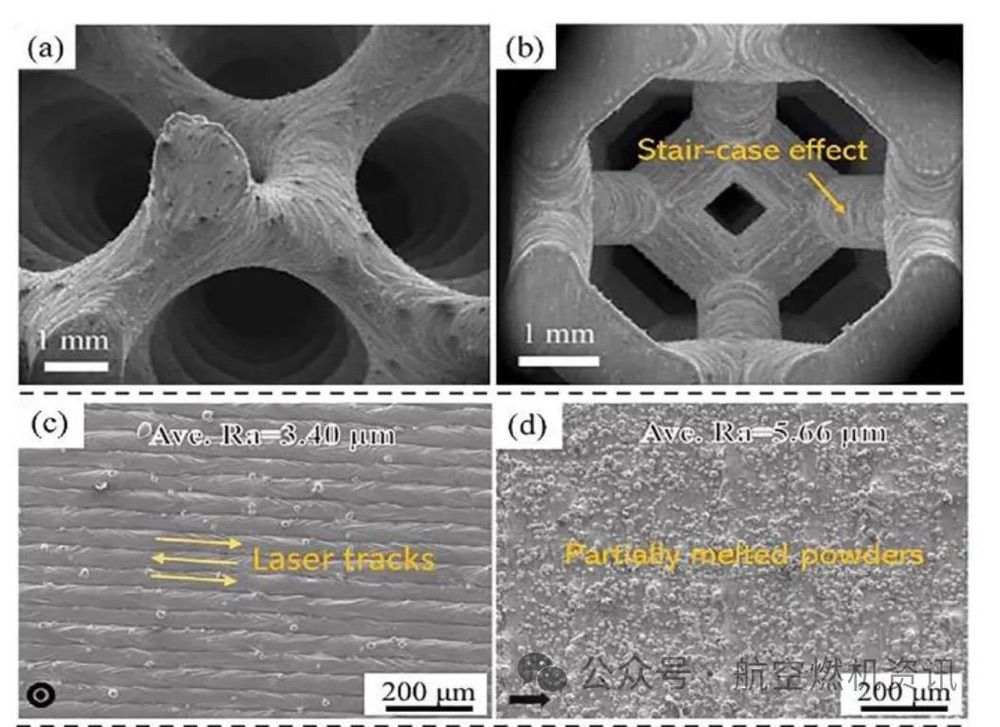
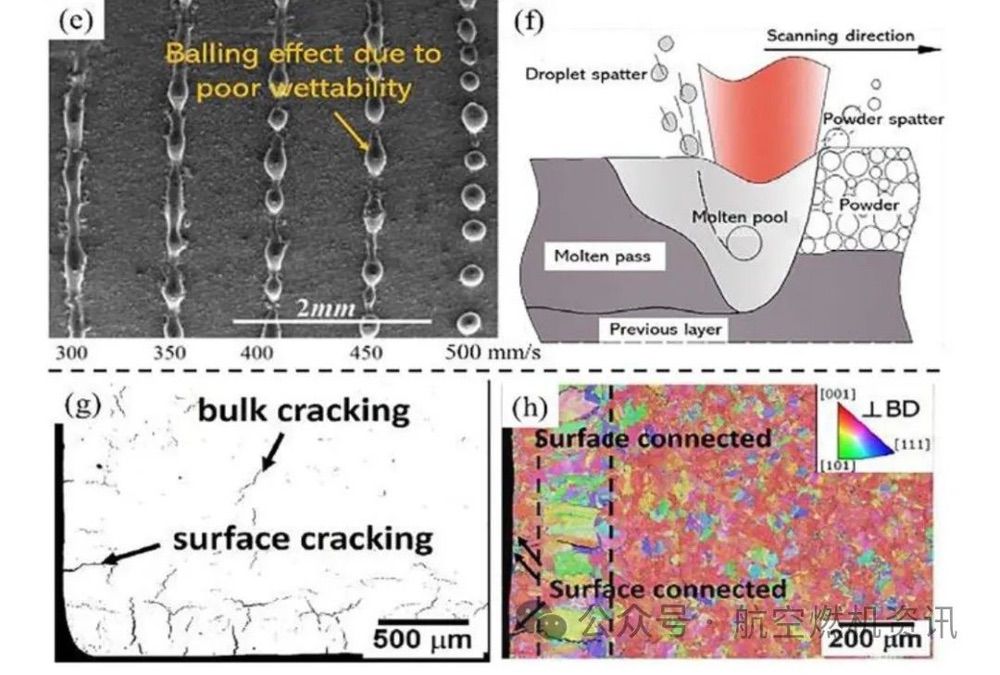
液球的形成。例如,在图 (e)中,随着激光扫描速度的增加(能量输入的减少),熔池被拉长。伴随着润湿性的降低,它往往会破裂成不连续的小球。在一定程度上增加能量输入,可以改善润湿性,抑制成球效应。然而,过多的能量输入可能会因液滴飞溅而再次诱发成球效应,如图 (f)所示。如此高的能量密度会产生不稳定的熔池,伴随着金属的蒸发和较大的反冲压力,致熔化的金属和未熔化的粉末飞溅。溅落的液态金属形成微尺度的凝固球体落在表面上。由于液体的低粘度和长寿命,这种液滴飞溅诱导的球化效应在高激光功率和低扫描速度的条件下普遍存在。而且,球化效应不仅会导致表面粗糙度增加,还会导致金属粉末沉积不均匀,并可能诱发孔隙和分层。
最后但并非最不重要的是,表面裂纹也是一个需要关注的关键缺陷。Tang 等在 SLM 制造 CM247LC 时采用边界扫描策略,旨在提高表面光洁度。虽然使用边界扫描策略获得了光滑的表面但结果表明,与体块区域相比,边界区域存在更多的裂纹,如图(g)所示。随后,作者检查了边界区和体区晶体结构,分别以粗柱状晶粒和细长织构晶粒为特征,如图 (h)所示。表面裂纹沿边界区域的高角度晶界出现。边界区较大的柱状晶粒与高密度的几何必要位错(GND)有关,这意味着更高的内应力,从而更高的裂纹敏感性。因此,在表面光洁度和表面附近区域的裂纹之间的权衡是裂纹敏感合金(如镍基高温合金)的 AM 的关键问题。需要同时考虑这些因素对工艺参数进行仔细优化。
(责任编辑:admin)
最新内容
热点内容